7 Tips for Designing Corrosion-Resistant Metal Parts
Corrosion is a major challenge when using metal components for industrial and commercial applications. It causes material degradation, which can reduce strength, pose safety risks, and increase maintenance costs.
Prioritizing corrosion resistance during the design process is essential for durability and long-term performance. This guide outlines practical tips for designing corrosion-resistant metal parts to promote efficiency and cost-effectiveness in your projects.
Why Corrosion Resistance Is Crucial
Corrosion-resistant designs promote the longevity and structural integrity of machinery, infrastructure, and equipment used across various industries. Otherwise, metals are likely to incur material degradation caused by environmental factors like moisture, chemicals, and extreme temperatures, causing premature failure.
Additionally, corrosion resistance contributes to cost efficiency by decreasing the need for frequent repairs, replacements, and maintenance. Corrosion-resistant parts’ enhanced performance and durability make them indispensable in industries such as aerospace, construction, and marine applications, where harsh operating conditions demand highly reliable materials.
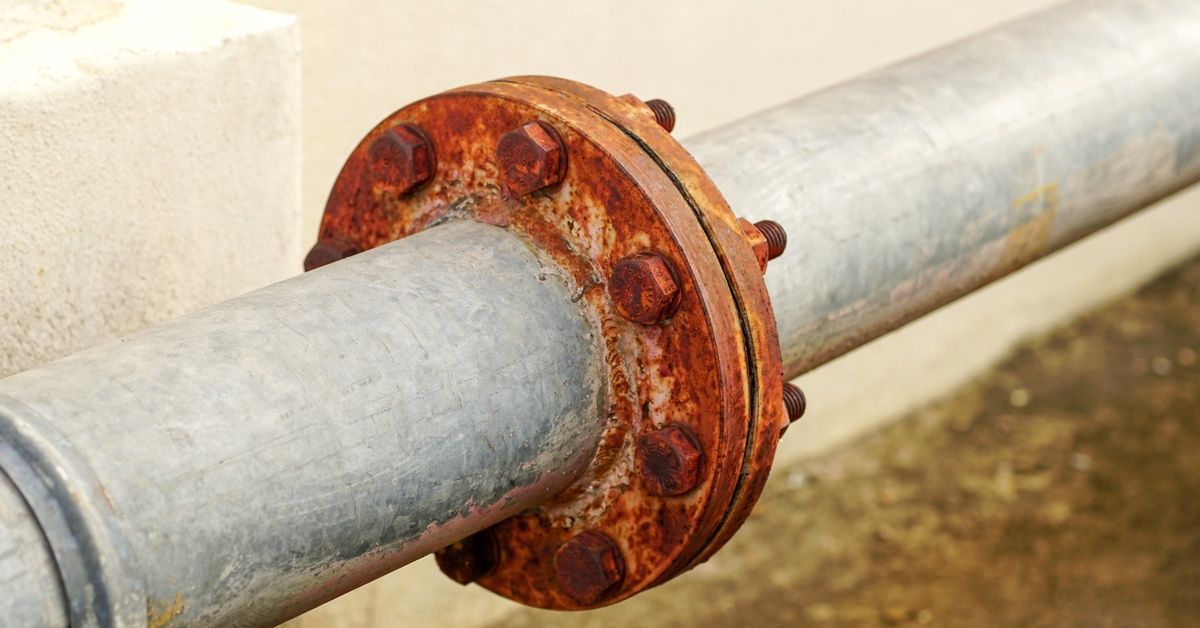
Select the Proper Material
Choosing the right material is a critical first step when designing corrosion-resistant metal parts. Materials vary in their ability to withstand corrosive environments, and selecting the optimal fit for your application is essential.
Stainless Steel
Stainless steel is a preferred choice for its resistance to rust and corrosion in a broad range of environments. Its chromium content forms a passive oxide layer, protecting it from harmful elements like moisture and salt. For intricate or high-precision projects, opting for stainless steel fabrication services ensures proper handling and quality assurance.
Aluminum
Aluminum offers excellent corrosion resistance due to its natural oxide layer. It’s especially effective in settings that require lightweight materials, such as in aerospace and automotive industries. While not as strong as stainless steel, its durability and resistance make it versatile for many projects.
Titanium
Titanium is known for its exceptional strength-to-weight ratio and excellent corrosion resistance. This metal excels in extreme environments, including those exposed to salt water or chemical agents. While more expensive, titanium’s durability often outweighs the initial cost in demanding applications.
Copper Alloys
Copper and its alloys, such as brass and bronze, offer natural corrosion resistance. These materials are frequently used in plumbing, electrical, and architectural applications. With proper design, they maintain their visual appeal and structural integrity over time.
Consider the Use Environment
The environment influences how a metal part responds to corrosion. Factors like humidity, temperature, and exposure to chemicals or salty air can accelerate corrosion by creating an environment where metals are more prone to oxidation.
Additionally, environmental mechanical stress, such as vibrations or physical impacts, can create microcracks that make metals more vulnerable to corrosion over time. During the design phase, account for these variables by selecting materials and finishes with suitable corrosion-resistant properties for the intended use environment.
Apply Protective Coatings
Protective coatings are an effective method to shield metal parts from corrosive elements. Coatings act as a barrier between the material and its environment, reducing the risk of chemical interactions that might lead to corrosion.
Painting
Applying a high-quality paint coating forms a protective layer that prevents moisture and oxygen from coming into direct contact with the metal’s surface. Proper preparation before painting, such as cleaning and priming the surface, increases the paint’s durability.
Powder Coating
Powder coats provide a thicker, more durable protective layer compared to traditional paints. The coat goes on like a dry powder and then is heated, creating a tightly bonded finish. Powder coating enhances a part’s durability and aesthetic appeal, making it ideal for visible metal components.
Galvanization
Galvanizing adds a zinc layer over metal parts, which sacrifices itself to protect the underlying material from corrosion. This technique is commonly used for parts in heavy-duty industries requiring extended longevity.
Optimize Part Geometry
The geometry of a part affects its susceptibility to corrosion. For example, improperly sealed joints, deep crevices, or features that can trap moisture or restrict airflow are more prone to corrosion over time. Designing parts with proper drainage and smooth surface transitions reduces areas where moisture and contaminants can collect. These design choices help improve the component’s durability and corrosion resistance, especially in harsh conditions.
Use Corrosion-Resistant Fasteners
Fasteners, though small, can be a weak point in corrosion-resistant designs if not carefully selected. Additionally, mismatched materials between fasteners and the primary part material can lead to galvanic corrosion, resulting in visible powdery deposits, pitting, or deterioration at the points of contact where the materials interact.
Using fasteners made from matching corrosion-resistant materials, like stainless steel or titanium, or adding spacers to separate materials helps the entire assembly maintain its integrity. Choose fasteners designed for your specific application and material to achieve consistent performance and reduced maintenance costs.
Utilize Proper Surface Treatments
Surface treatments enhance the durability and corrosion resistance of a wide range of metal parts. These treatments are applied to improve the material’s ability to withstand adverse conditions and extend longevity.
Anodization
Anodizing is primarily used for aluminum parts, adding a thick oxide layer that drastically improves corrosion resistance. The treatment generates a porous outer surface that can be dyed or sealed for additional protection.
Electroplating
Electroplating involves applying a thin layer of another metal, such as chrome or nickel, to the surface of the part. This treatment adds strength and resistance against wear and corrosion, making it an excellent option for parts subject to friction or harsh conditions.
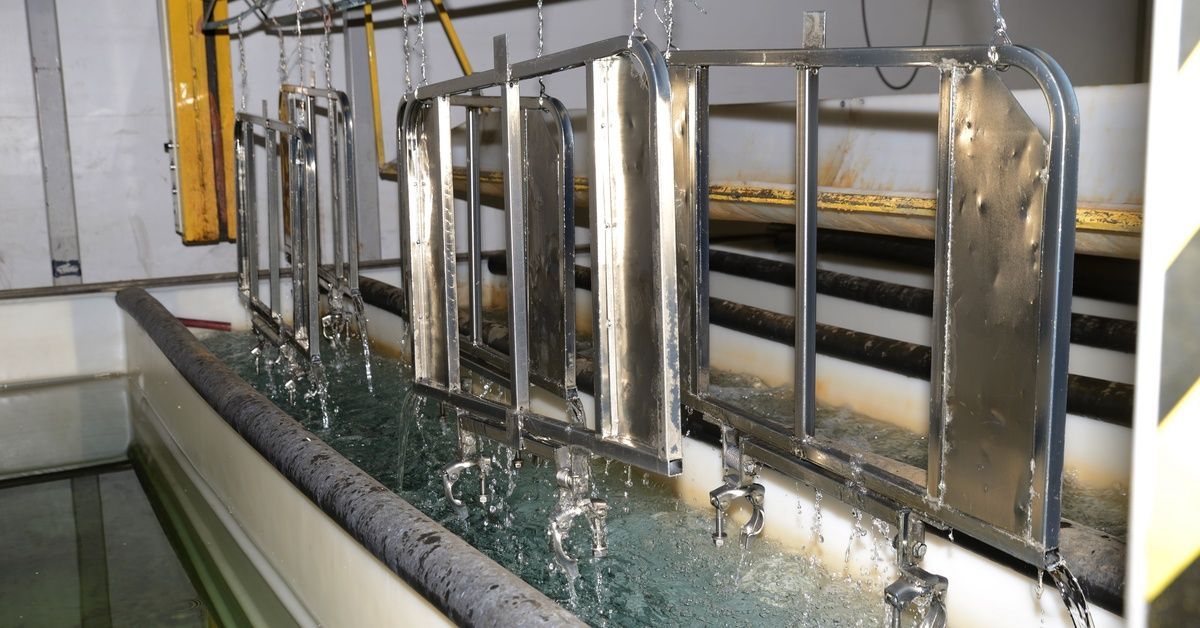
Phosphate Coatings
Phosphate coatings, particularly zinc phosphate, create a textured surface that improves paint and primer adhesion. These coatings also provide corrosion resistance and lubrication, making them a popular choice for industrial applications.
Test Parts for Quality Assurance
Finally, testing metal parts for quality assurance ensures that they meet the required standards for corrosion resistance. Conducting laboratory tests and simulations under controlled conditions validates the design and material choices made during manufacturing.
Testing methods like salt spray, electrochemical, and cyclic testing evaluate material durability and performance, allowing adjustments before widespread deployment. By investing in quality assurance, you safeguard your project against unforeseen costs and potential failures.
Invest in Corrosion-Resistant Longevity
Corrosion resistance is essential for the durability and operational efficiency of metal parts. From material selection to applying protective coatings and implementing surface treatments, effective design strategies are key. By following the tips for designing corrosion-resistant metal parts outlined in this guide, you can confidently create parts that withstand harsh environments and serve their intended purpose for years to come.
For expert assistance in creating corrosion-resistant designs, contact James Manufacturing. We have over 45 years of experience in designing and manufacturing long-lasting metal components for businesses in North Texas, so call us today.