Aluminum CNC Machining: A Complete Guide
CNC machining has become a primary manufacturing method across many industries, offering unparalleled precision and efficiency in creating complex parts. Due to its unique properties, aluminum has solidified its position as one of the most popular materials for CNC-machined parts. This complete guide to aluminum CNC machining will provide an overview of aluminum’s benefits, explore commonly used aluminum alloys, and outline key machining and post-machining processes.
Benefits of Aluminum for CNC-Machined Parts
Here are the leading reasons aluminum is a predominant choice for CNC machining.
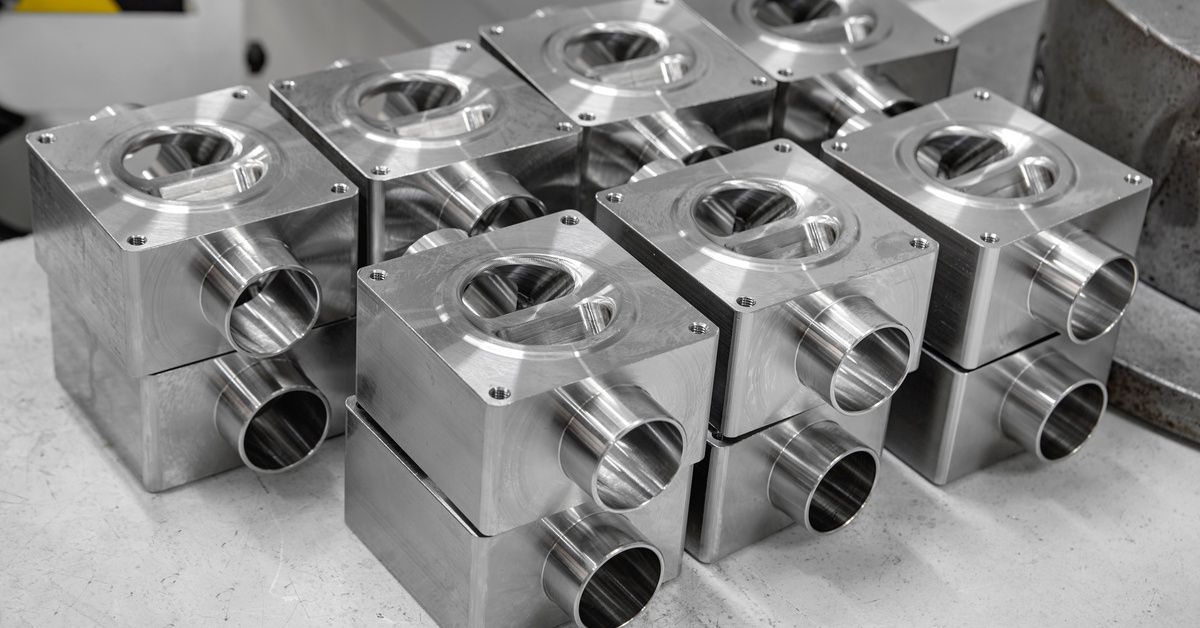
Machinability
Aluminum is known for its excellent machinability, which refers to its ability to be shaped and cut with precision during the CNC machining process. It can be drilled and shaped with less effort compared to harder metals like steel or titanium, resulting in faster production cycles and reduced tool wear. Aluminum’s properties minimize the risk of component deformation, allowing manufacturers to meet tight tolerances with greater accuracy.
Strength-to-Weight Ratio
Aluminum boasts an impressive strength-to-weight ratio, offering high structural integrity without too much added weight. With only one-third the density of steel, aluminum is particularly advantageous in industries such as aerospace and automotive, where reducing weight can greatly enhance performance and energy efficiency. Aluminum is durable and lightweight, offering a unique balance that other metals cannot achieve.
Corrosion Resistance
Another notable feature of aluminum is its natural corrosion resistance. When exposed to air, the metal forms a protective oxide layer, which shields it from environmental factors such as moisture and oxidization. Aluminum parts have longer lifespans with minimal maintenance for applications requiring high durability in harsh conditions.
Electrical Conductivity
Aluminum also boasts an excellent electrical conductivity of around 37.7 million Siemens per meter (S/m) at room temperature, making it a popular choice for electrical and electronic components. While not as conductive as copper, aluminum offers a more cost-effective alternative for applications where conductivity is essential but cost or weight is a concern, such as electrical enclosures or heat sinks.
Recyclability
Aluminum’s recyclability makes it a sustainable choice for CNC machining. The recycling process consumes less energy than new aluminum production, reducing costs and environmental impacts. These factors are crucial for CNC machining, as its subtractive operation decreases excessive waste and leftover material.
Commonly Used Aluminum Alloys
Selecting the right aluminum alloy for CNC machining depends on the desired application, as each alloy has its own set of strengths and limitations. Below is a breakdown of commonly used aluminum alloys, highlighting their key traits.
Aluminum 5083
Known for its exceptional corrosion resistance, aluminum 5083 is frequently used in marine and chemical applications. Its high strength and weldability also make it ideal for applications that demand substantial structural integrity without compromising maintainability. However, this alloy is unsuitable in temperatures above 65 degrees Celsius or 149 degrees Fahrenheit.
Aluminum 6060
Aluminum 6060 offers excellent corrosion resistance and is often used for applications requiring good weldability, such as architectural frames and piping. Its machinability is moderate, though not as high as that of 6061, and it delivers reliable performance for projects that do not require extreme mechanical strength.
Aluminum 6061
Aluminum 6061 is one of the most versatile aluminum alloys, offering a balanced combination of good machinability, strength, and corrosion resistance. Its applications include automotive parts, aerospace components, and construction materials. Though slightly less strong than alloys like 7075, its overall performance and adaptability make it a preferred choice for many industries.
Aluminum 6082
Aluminum 6082 is a structural alloy widely used in construction and marine applications. It delivers excellent corrosion resistance, reasonable strength, and weldability. While closely related to 6061, 6082 exhibits slightly superior strength, but this may come at the cost of reduced machinability when compared to other alloys commonly used in CNC machining.
Aluminum 7075
Aluminum 7075 is renowned for its strength and hardness, often exceeding that of mild steel. It’s ideal for high-performance applications such as aerospace and military-grade components, as well as some sporting equipment. However, its higher cost and lower corrosion resistance make it less practical for long-term projects exposed to harsh environments.
Aluminum CNC Machining Processes
Different CNC machining methods are used to shape aluminum parts. The choice of method depends on the design’s complexity, required tolerances, and end-use application.
Milling
Milling is a CNC machining process that uses rotary multipoint cutting tools to remove material from a workpiece and shape it into the desired form. The tools move along multiple axes to achieve complex geometries and precise dimensions while the workpiece remains stationary or rotates along its own axis. Aluminum’s machinability makes it perfect for efficiently milling intricate designs, custom components, and high-volume parts.
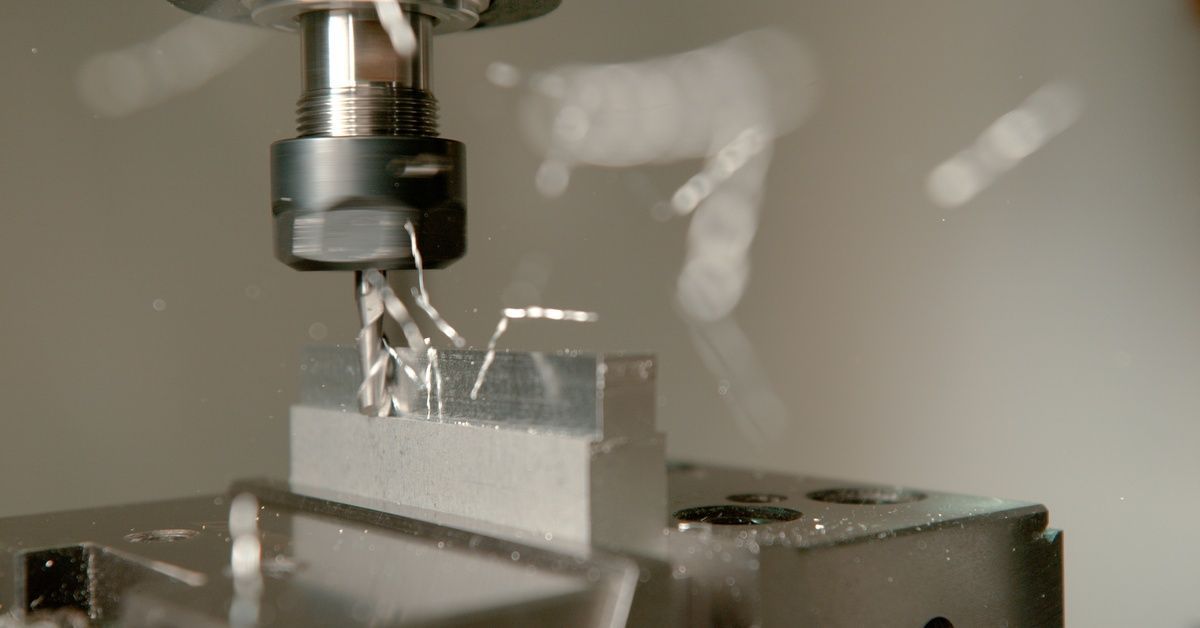
Turning
Turning is when an aluminum workpiece is rotated on a lathe while stationary single-point cutting tools shape it. Either the workpiece or the cutting tool can perform the feed motion to allow for precise material removal, producing cylindrical parts with accurate dimensions and smooth surface finishes. The process is highly efficient for creating shafts, bushings, and other round components.
Drilling
Drilling is the process of creating holes in aluminum workpieces by using a rotating drill bit. The bit moves in a straight line perpendicular to the material at specific locations and depths for accuracy and repeatability. Holes present in aluminum CNC workpieces typically accommodate screws and bolts for later assembly.
Post-Machining Aluminum Processes
Post-machining finishes improve the appearance and performance of CNC-machined aluminum parts. The following processes are often applied to achieve the desired results.
Sandblasting
Sandblasting is a surface finishing process where abrasive particles are blasted at aluminum parts to remove imperfections or machining marks. It results in a smooth, matte finish with a uniform texture. This process is ideal for improving the appearance of parts and preparing surfaces for further treatments.
Powder Coating
Powder coating involves applying a dry powder to aluminum parts with an electrostatic spray gun, which is then cured under heat to form a protective layer. This method adds durability for less wear and protection against corrosion. Powder coating is perfect for parts exposed to harsh environments or those requiring vibrant finishes in various hues.
Anodizing
Anodizing is an electrochemical process that creates a durable, corrosion-resistant oxide layer on aluminum surfaces. This coating enhances hardness and protects against wear while allowing for color customization. Anodized surfaces are also ideal for improving paint and coating adhesion.
Unlocking the Full Potential of Aluminum CNC Machining
As this guide to aluminum CNC machining shows, aluminum is one of the most versatile and widely used materials for CNC machining, combining machinability, strength, and sustainability in a way few materials can match. Whether you’re designing aerospace parts, marine components, or everyday consumer goods, the right choice of aluminum alloy and machining processes can elevate your project’s success.
James Manufacturing offers custom CNC machining for aluminum and other materials, using industry-leading technology to craft intricate components. Our team has experience machining parts across various industries, serving customers throughout the Dallas-Fort Worth metroplex. Contact us today to discuss how we can assist you with your aluminum CNC machining needs.