The Most Common Materials Used in Metal Fabrication
From towering skyscrapers to intricate jewelry, metal fabrication transforms raw materials into usable forms. No matter the type of project, material selection can determine the durability, cost, and functionality of the final product.
This post offers a deep dive into the most common materials used in metal fabrication, exploring their unique properties and applications. Whether you’re a business owner, a craftsperson, or someone who’s simply curious about how the process works, this guide is for you.
Common Metal Fabrication Materials
Steel
Steel is a versatile, durable material preferred for its excellent mechanical properties. It’s known for its high strength, ductility, and resistance to wear and corrosion. These attributes make steel suitable for various industrial and consumer applications. Each type of steel is tailored for specific purposes, offering unique qualities dependent on the composition and intended use.
Carbon steel is the most common type found today. Characterized by its high strength and affordability, it’s primarily used in construction and manufacturing. Stainless steel is widely featured in medical equipment, kitchenware, and architectural components due to its corrosion resistance. Alloy steel includes various elements like chromium, nickel, or molybdenum, enhancing its strength and resistance to heat and wear.
Aluminum
Aluminum is a lightweight, corrosion-resistant metal known for its versatility and durability. It’s highly malleable, making it easy to form into various shapes, and possesses a natural oxide layer that enhances its rust resistance. Additionally, aluminum is nontoxic, conductive, and recyclable, making it an eco-friendly material widely used across industries.
Pure aluminum is soft and ductile, often used in applications where flexibility and corrosion resistance are crucial, such as electrical wiring and food packaging. Aluminum alloys, on the other hand, are combined with elements like copper, magnesium, or silicon to improve strength and mechanical properties. These alloys are commonly used in automotive, aerospace, and structural industries due to their enhanced performance.
Copper
Copper is a widely used metal known for its electrical and thermal conductivity. It’s highly pliable for applications in electrical wiring, plumbing, and roofing. Copper also offers natural corrosion resistance, which is further enhanced by the development of a protective patina over time.
Its aesthetically pleasing reddish-gold appearance often makes it a popular choice for decorative elements and architectural designs. Additionally, copper alloys like bronze and brass expand the metal’s utility.
Brass
Brass is an alloy primarily composed of copper and zinc, with the proportions of each element varying to achieve specific mechanical and electrical properties. Known for its bright, golden appearance, brass is a favored material in decorative applications, including musical instruments, fixtures, and jewelry.
Beyond aesthetics, brass boasts great machinability, corrosion resistance, and thermal conductivity, making it a versatile choice for industrial purposes such as fittings, valves, and bearings. Its antimicrobial properties also make it valuable in environments requiring hygiene and sanitation.
Titanium
Titanium is a lightweight, highly durable metal known for its exceptional strength-to-weight ratio. It has corrosion resistance, even in extreme environments such as seawater and chlorine exposure, making it invaluable in aviation, marine, and chemical applications. Titanium is also biocompatible, meaning it’s nontoxic and doesn’t react with the human body, which is why it’s often used in medical implants and prosthetics.
Additionally, its ability to withstand extreme temperatures makes titanium a preferred material in aerospace engineering. Despite being more expensive than some other metals, its unique properties ensure titanium remains an essential material.
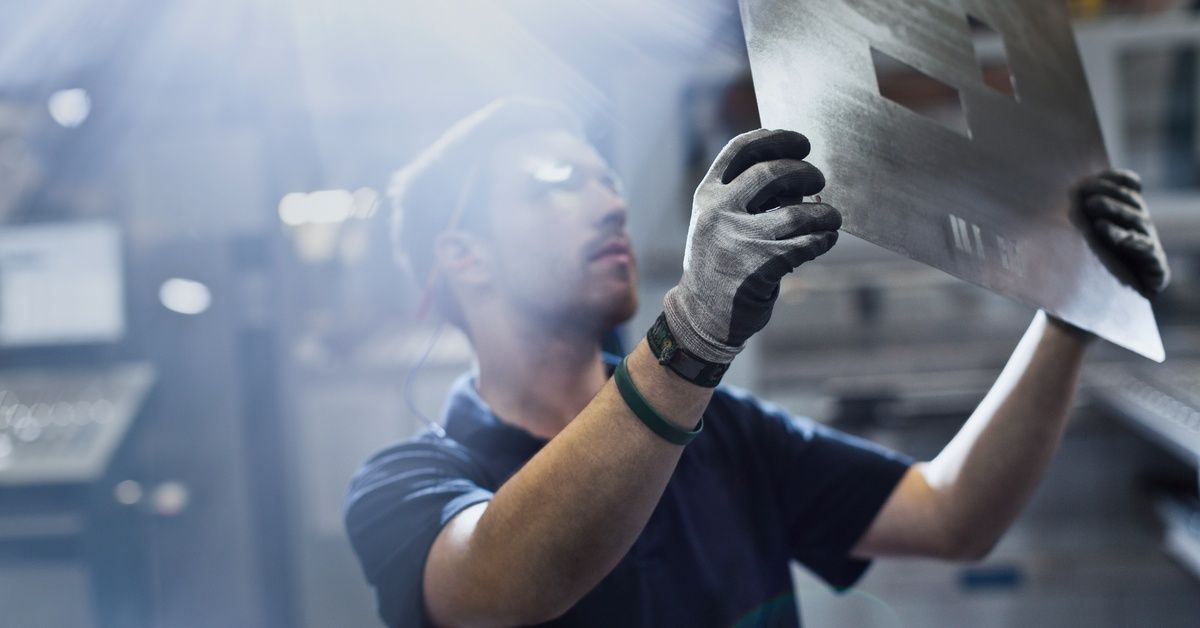
Metal Fabrication Uses Across Industries
These industries rely the most strongly on metal fabrication:
Construction
The construction industry uses metal fabrication for structural components like beams, columns, and roofing. Metal is also common in infrastructure projects, such as bridges, railings, and staircases, providing strength and durability.
Automotive
Metal fabrication plays a critical role in the automotive industry by supplying components like chassis, body frames, and exhaust systems. Precision and strength are vital for vehicle safety and performance.
Aerospace
The aerospace industry uses metal fabrication to produce lightweight, highly durable components for aircraft, rockets, and spacecraft. Manufacturers in this sector often need custom engine parts, fuselages, and landing gear.
Manufacturing
Manufacturers depend on metal fabrication for tools, machinery, and equipment essential to production processes. This includes everything from conveyor systems to industrial robots.
Energy Sector
Metal fabrication supports the energy sector through the creation of pipelines, wind turbines, and solar panel frames. These components provide efficient energy production and distribution.
Consumer Goods
Everyday products like appliances, furniture, and electronics also rely on metal fabrication. Processes like stamping and welding are two examples that create durable parts for consumer use.
With such diverse applications, choosing the right material for metal fabrication ensures that the end product is effective and reliable.
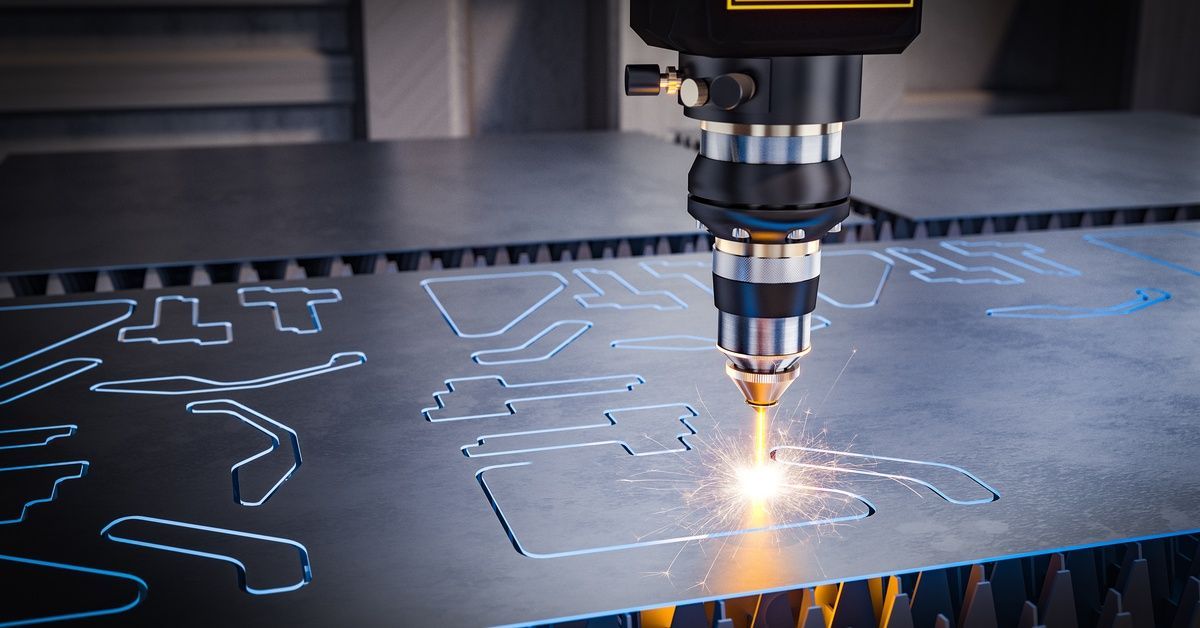
Factors To Consider When Choosing a Metal
Selecting the right metal depends on factors specific to the intended use case. Consider the following factors when deciding:
- Strength and durability: Evaluate the required strength and durability of the metal for its intended application to ensure it can withstand stress and wear.
- Corrosion resistance: Consider the metal’s resistance to corrosion, especially if it will be exposed to moisture, chemicals, or extreme environmental conditions.
- Weight: Take into account the weight of the metal, particularly in applications where lightweight materials are crucial, such as aerospace or portable products.
- Cost: Analyze the cost of the metal, balancing affordability with quality and long-term performance.
- Appearance: Factor in the aesthetic appeal of the metal, especially for applications where design and visual appeal are important.
- Workability: Assess the ease with which the metal can be shaped, welded, or machined depending on the complexity of the design.
Why Outsource Metal Fabrication?
Outsourcing metal fabrication offers advantages for businesses seeking efficiency and cost-effectiveness. By partnering with specialized fabrication companies, businesses can access advanced equipment and expertise without the need for large investments in machinery or training. This approach can reduce operational costs, streamline production processes, and maintain high-quality results.
Additionally, outsourcing allows companies to focus on their core operations while meeting tight deadlines and accommodating fluctuating project demands. With access to skilled professionals and cutting-edge technology, outsourcing metal fabrication provides a reliable solution for producing complex and precise metal components.
Choose the Right Materials for Your Next Project
With so many options, it’s easy to get lost in the nuances of a big project. By exploring the most common materials used in metal fabrication, you can make a decision that fits your current needs and long-term business model.
Are you ready to get your metal fabrication project completed? James Manufacturing is here to help. Our custom metal fabrication services will meet your specific qualifications so you can get things done faster and more efficiently. By selecting wisely and leveraging the expertise of metal fabrication professionals, you can optimize your operations and find success.