How Reverse Engineering Benefits Manufacturers
Reverse engineering is far from being just another tool in the toolbox. It’s a multifaceted gem providing substantial advantages to manufacturers who are ready to harness its capabilities fully.
This process involves taking a part or machine and breaking it down so that you can assess everything about it. You’ll learn how it works, which parts are outdated, and how you can make improvements. All this and more is accomplishable through reverse engineering. Learn how reverse engineering benefits manufacturers so that you can stay at the forefront of innovation and efficiency in the workplace.
Elevating Product Quality and Reliability
The meticulous process of reverse engineering provides unique insights into products, revealing areas of vulnerability and opportunities for quality enhancement. By addressing these discoveries, manufacturers can develop products that are superior in performance and exceed reliability expectations, thereby fostering stronger customer trust and loyalty.
Plus, reverse engineering is the catalyst for creating a digital twin of physical products, which acts as the backbone for efficient product lifecycle management (PLM). This process enables manufacturers to swiftly adapt to changes, anticipate maintenance, and improve product longevity, ensuring a product's relevance from conception to retirement. The closer you look at products or equipment, the easier it is to understand how they work. This can help when you need to complete repairs or replacements that keep them working productively.
Keeping Older Equipment Alive
Unfortunately, although a machine may keep working well in the workplace, the parts you need to complete maintenance or repairs may not be readily available. With older machines, it’s easy to find yourself struggling to find new replacement parts. Luckily, reverse engineering old components will help you find a custom solution and a consistent supply of new components.
A reliable manufacturer upgrades its manufacturing process by reverse engineering obsolete machinery components, giving new life to classic and rare industrial machines. This is a key reason you should work with a reliable, accurate machining service for this task. Downtime is a major hindrance to workflow. So having a machining service by your side that can always help you get quick, quality replacement parts is critical to workplace efficiency.
Using Strategic Cost Reduction
Another important way that reverse engineering benefits manufacturers is by helping reduce costs in the right places. After all, cutting costs and compromising the quality of the product isn’t ideal, so reverse engineering helps with making strategic cost-reduction choices.
In industries where the development process from ideation to market introduction is both time-consuming and expensive, reverse engineering offers a strategic pathway to cost efficiency. By analyzing and improving existing products, manufacturers can significantly cut down on R and D expenses. This approach allows for the allocation of resources to other critical areas, such as marketing, customer service, or further innovation.
Plus, identifying areas worth improving ensures you don’t create a product that functions inadequately. Simply put, reverse engineering ensures you can get products working as effectively as possible to prevent them from breaking down and requiring costly replacements.
You can start reverse engineering parts today if you’re ready to reap the benefits above. Contact our team at James Manufacturing to schedule custom CNC machining services that specialize in reverse engineering and other techniques that’ll help you assess and develop high-quality parts.
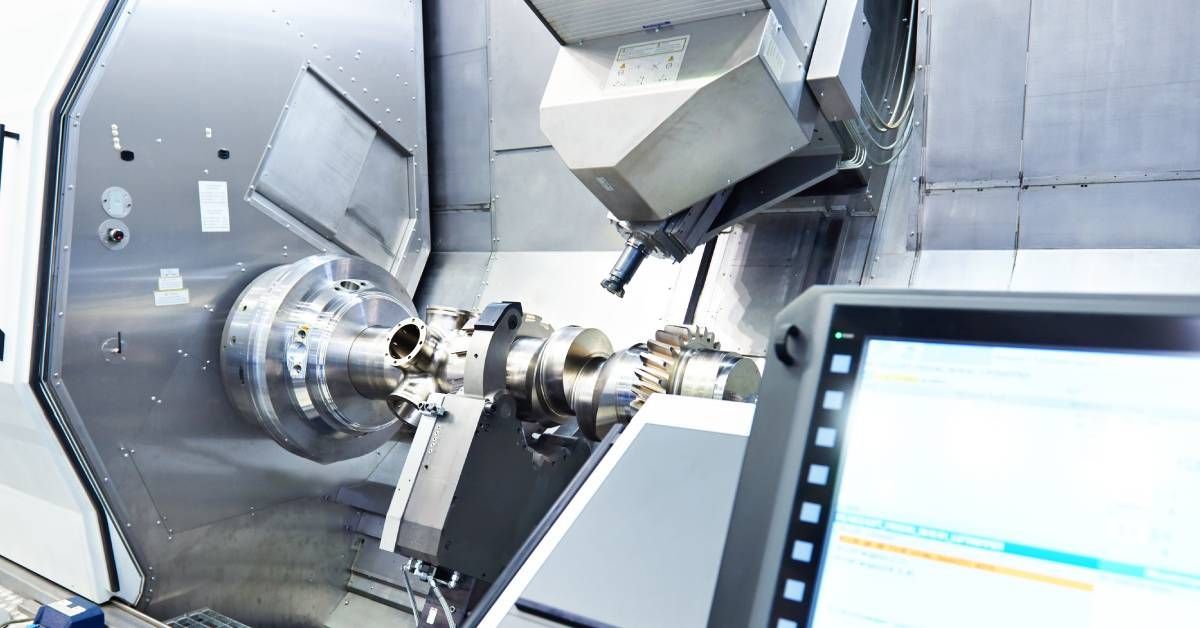