CNC Machining vs. Conventional Machining
Machining is an essential process in the manufacturing industry, transforming raw materials into precise, functional components for countless use cases. Whether building aerospace parts or crafting intricate medical devices, machining plays a critical role. But should you use CNC machining or conventional machining for your next project?
Both methods have their strengths and weaknesses, which can make choosing the right option a challenge. To make the decision easier, we’ll discuss CNC machining vs. conventional machining, highlighting their biggest differences. By the time you’re done reading, you’ll have a solid grasp of which technique suits your needs.
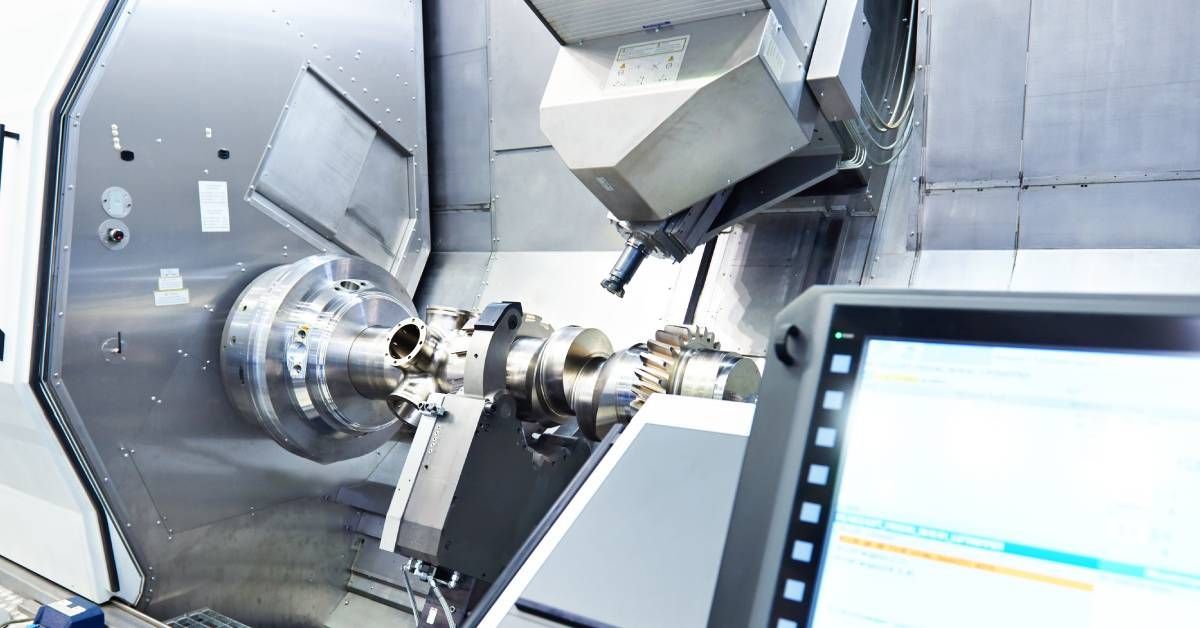
The History of Conventional and CNC Machining
The Origins of Conventional Machining
Machining has a rich history that can be traced to the early days of manufacturing. Conventional machining, in its simplest form, dates to the 18th and 19th centuries during the industrial revolution.
Early machinists relied on manually operated lathes, milling machines, and grinders to shape materials. These machines required skilled operators to carefully guide tools by hand for precision through years of honed expertise. Although effective, the process was time-consuming and often limited by human accuracy.
Enter CNC Machining
The introduction of Computer Numerical Control (CNC) in the mid-20th century revolutionized machining. The idea was born from the desire to automate and increase efficiency in manufacturing. Early CNC machines emerged in the 1950s, harnessing rudimentary computational power to control machine tools.
Over the decades, advancements in computing and software technology transformed CNC machining into the highly accurate, automated process we know today. With the ability to program highly intricate designs and operate continuously with minimal human intervention, CNC machining has expanded production capabilities across various industries, setting a new standard in precision engineering.
Understanding Conventional Machining
Conventional machining employs manually operated tools such as lathes, mills, and drill presses to shape materials. Skilled operators use their hands and expertise to control the process and achieve the desired results.
The Advantages of Conventional Machining
- Cost-effective for small production runs: Conventional machining is an economical choice for small-scale projects or prototypes, as it avoids the high setup costs associated with CNC machining.
- Flexibility in customization: Skilled operators can make real-time adjustments during the machining process, providing greater adaptability for unique or complex designs.
- Lower initial investment: Since conventional machines are generally less expensive than CNC machines, they can be a more viable option for smaller workshops or businesses with budget constraints.
- Hands-on skill development: Conventional machining requires operators to develop and refine their manual skills, fostering a deep understanding of material properties and manufacturing techniques.
- Simplicity of maintenance: Traditional machines are often mechanically simpler and easier to maintain compared to CNC machines, which require more specialized technical expertise.
Projects That Require Conventional Machining
- One-off prototyping: Conventional machining is ideal for creating custom prototypes in low quantities where CNC programming is not cost-effective.
- Repair work: Manual machining is often preferred for repairing or modifying existing components, especially when the work requires adaptability and precision by hand.
- Artisanal or decorative items: Traditional machines are suited for crafting intricate, handcrafted items such as jewelry, sculptures, or decorative components.
- Small-batch production: Conventional machines are best for producing small batches of parts, where setting up a CNC machine would take longer than manual machining.
- Teaching and training: Conventional machines are commonly used in educational settings to teach machining fundamentals and hands-on skills.
While conventional machining has its benefits, some projects may be better off with the use of CNC equipment.
Understanding CNC Machining
CNC machining is a technology-driven process where computer software precisely controls machine tools to produce parts automatically. Engineers preprogram design data, and the CNC machine follows exact instructions to cut, drill, mill, or turn materials. This technology has revolutionized the manufacturing world by offering unparalleled speed, precision, and repeatability.
The Advantages of CNC Machining
- Precision and accuracy: CNC machines can achieve microscopic tolerances, ensuring high-quality, consistent results, even for large production runs.
- Speed and efficiency: Once programmed, machines can operate around the clock without breaks, significantly speeding up production.
- Complex geometries: CNC machining excels at creating complex shapes and designs that would be difficult or impossible with manual methods.
- Automation: Human intervention is minimized, reducing the risk of error and improving safety.
Projects That Require CNC Machining
- Medical devices: Surgical instruments, implants, and diagnostic equipment components benefit from CNC machines.
- Electronics housings: The enclosures for circuits, connectors, and other electronic assemblies come from CNC devices.
- Custom tooling: Molds, dies, and fixtures for use in various manufacturing processes rely on CNC machining.
- Consumer products: High-quality custom parts for products such as watches, instruments, and sporting equipment use CNC.
- Robotics: Precision parts for robotic arms, joints, and movement systems depend on this advanced machining.
Despite the benefits of CNC machining, you should consider the key aspects of each project before jumping in.
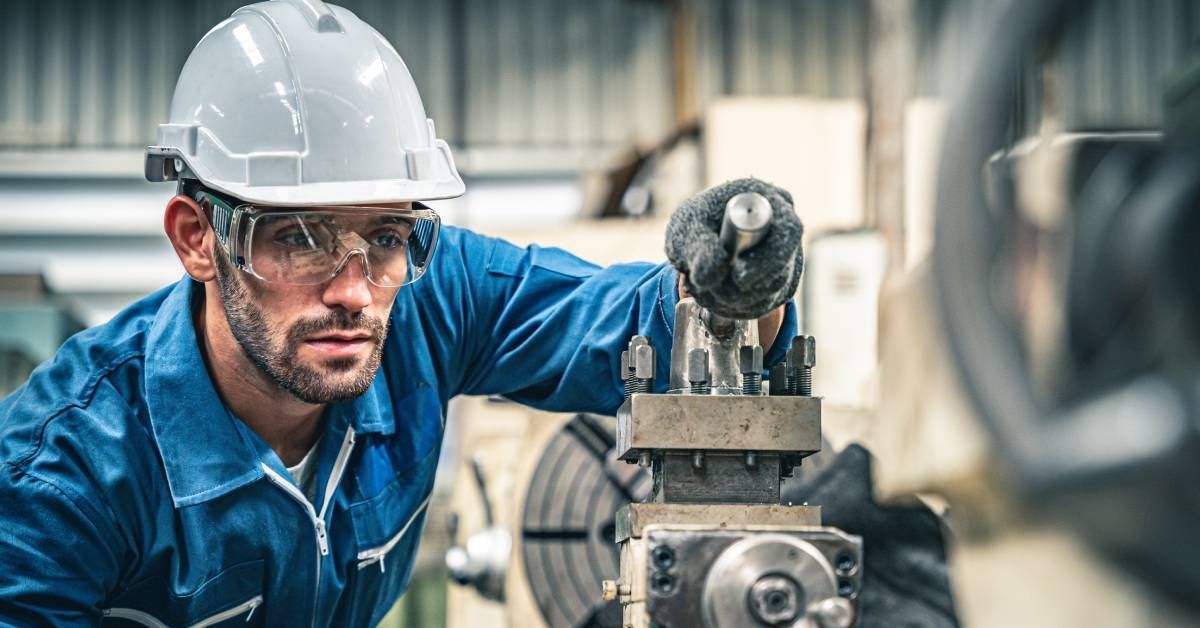
The Clash of Technologies: CNC vs. Conventional Machining
When deciding between CNC vs. conventional machining, it’s important to weigh the strengths and weaknesses of each method.
Here are a few key comparisons:
Cost
- CNC machining: This form of machining has a higher initial cost due to software, programming, and machine setup. However, it becomes cost-effective for large production runs.
- Conventional machining: Lower initial costs are appealing, but higher costs for high-volume or complex output due to labor intensity are a possibility.
Speed
- CNC machining: CNC machines are known for their fast, continuous operation with minimal downtime. Their automation can handle large workloads at unprecedented speeds.
- Conventional machining: These machines are slower since they rely on human intervention for adjustments and operation.
Accuracy
- CNC machining: CNC machines are highly accurate with exceptional repeatability for intricate, high-precision tasks.
- Conventional machining: Accuracy relies on operator expertise with traditional machines, making them less reliable for highly detailed components.
Complexity
- CNC machining: These machines easily produce complex, unconventional geometries.
- Conventional machining: This option is best when working on simpler parts requiring minimal cuts or contours.
Flexibility
- CNC machining: These machines require significant setup and programming for new designs, which can slow down flexibility.
- Conventional machining: Operators can quickly adapt processes without reprogramming, making this form of machining suitable for custom jobs or small-scale production.
With these factors in mind, you can make an informed decision based on your needs.
So, Which Is Better?
The decision is about determining which is better for your specific needs. Below are a few considerations to keep in mind:
Choose CNC Machining If:
- You need high volumes of consistent, precision-engineered parts.
- Your project involves complex geometries or a tight tolerance requirement.
- Speed and automation are critical to your goals.
Choose Conventional Machining If:
- You’re working on a one-time project or prototype.
- Flexibility, simplicity, and lower upfront costs are your priorities.
- The design does not require highly detailed or intricate cuts.
No matter which you choose, you should do so carefully to get the most out of your investment.
Finding Your Perfect Fit in Machining Solutions
CNC and conventional machining are vital across industries. When deciding between the two, analyze your project’s complexity, budget, and production scale. Both methods are invaluable in their own right, and the best choice depends entirely on your unique needs and priorities.
Still unsure which method is best for your business? At James Manufacturing, we offer custom CNC machine services that you can rely on to get the job done right. Our team of experts is here to help. Reach out today for tailored advice on your machining requirements!