An Overview of the Different Types of Industrial Coatings
This is a subtitle for your new post
Whether safeguarding against corrosion, adding aesthetic appeal, or improving functionality, industrial coatings are indispensable to modern manufacturing and construction.
This comprehensive guide is your overview of the different types of industrial coatings. We’ll discuss their applications and factors to consider when selecting a coating for your needs. By the time you’re done reading, you’ll have a well-rounded understanding of their relevance in today’s industries and insights into the emerging trends shaping their future.
What Are Industrial Coatings?
Industrial coatings are specialized layers applied to materials or surfaces to achieve specific protective, decorative, or functional purposes. Unlike standard household paints, industrial coatings are engineered to endure harsh conditions, resist wear, and meet the unique requirements of industrial processes.
Their formulations can include various resins, pigments, additives, and solvents to create robust solutions that meet the demands of heavy-duty applications like manufacturing, energy, and transportation.

Why Are Industrial Coatings Important?
Industrial coatings offer a range of benefits that go beyond providing a polished appearance. Here’s why their role is critical in different sectors:
- Protective shield: Industrial coatings are a barrier against environmental factors like chemicals, moisture, and UV rays, increasing the longevity of machinery, equipment, and infrastructure.
- Enhanced performance: Functional coatings improve the superficial properties of materials, such as offering nonstick or thermal resistance capabilities.
- Aesthetic value: These coatings can add to the visual appeal of buildings or equipment by incorporating vibrant colors and finishes.
- Cost efficiency: By preventing frequent replacements and repairs, industrial coatings help companies save money over time while adhering to sustainability goals.
From oil rigs to skyscrapers, industrial coatings are the invisible guardians enabling structures and equipment to thrive in challenging conditions.
Types of Industrial Coatings
Industrial coatings can be broadly categorized into protective, decorative, and functional types, each serving unique purposes within industrial settings.
Protective Coatings
Protective coatings are designed to preserve surfaces from environmental degradation and mechanical wear for safety and longevity.
Anticorrosion Coatings
One of the most common applications of industrial coatings, anticorrosion products are essential in industries like marine, oil and gas, and construction. These coatings prevent rust and oxidation of metal surfaces exposed to moisture and oxygen. Both epoxy and zinc-rich coatings are widely used for this purpose.
Fire-Resistant Coatings
Fire-resistant coatings provide enhanced safety by protecting structures during fire-related incidents. These intumescent coatings expand when exposed to extreme heat, creating an insulating layer that delays surface temperature increases. They are often applied to steel structures in commercial buildings and pipelines.
Decorative Coatings
While protective qualities may be a priority, industrial settings also use coatings to boost visual appeal.
Aesthetic Coatings
Decorative coatings impart color, texture, and gloss to materials, elevating their aesthetic qualities. Commonly used in the automotive and architectural sectors, these coatings make surfaces visually appealing while often adding a layer of durability.
Color-Coded Coatings
Designed for practical applications, such as marking specific equipment or zones in industrial facilities, these coatings help visually organize workflows and minimize risks. Think of yellow paint used on safety rails or red paint reserved for hazard warnings.
Functional Coatings
Functional coatings offer specialized features that enable applications across industries requiring advanced performance capabilities.
Nonstick Coatings
Particularly popular in food manufacturing and cookware production, nonstick coatings enhance efficiency by reducing material adhesion to surfaces. These coatings often leverage fluoropolymer technology.
Thermal Barrier Coatings (TBC)
TBCs are engineered to insulate equipment from extreme thermal environments. Frequently used in automotive engines or industrial turbines, these coatings enhance performance and energy efficiency by managing heat distribution.
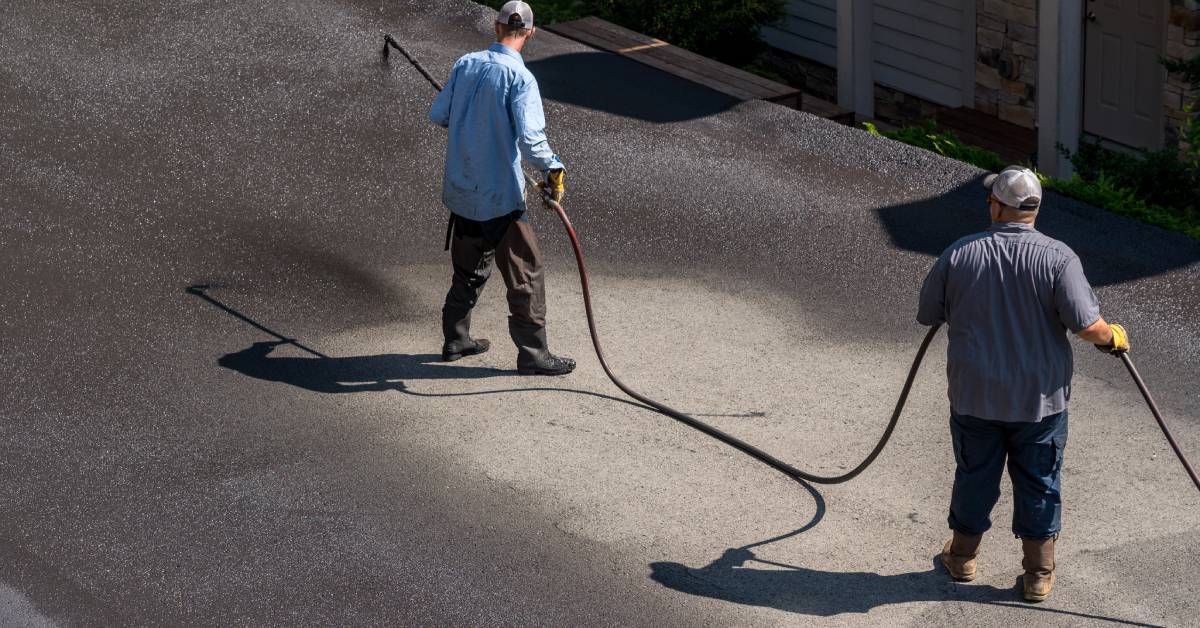
Factors To Consider When Selecting Industrial Coatings
With so many use cases, decision-makers have a lot to think about when deploying industrial coatings in professional settings.
Surface Material
The type of material being coated plays a crucial role in the selection process. Metals, plastics, concrete, and wood all have different chemical properties that require tailored coatings for optimal adhesion and performance.
Environmental Conditions
Understanding the level of environmental exposure, such as temperature extremes, UV radiation, humidity, or corrosive substances, determines the coating’s suitability for long-term durability.
Application Process
The ease and method of application—whether spraying, brushing, or dipping—impact the choice of coating. Factors such as drying time and required application equipment also need consideration.
Performance Requirements
Industrial coatings should meet specific functional needs, such as corrosion, abrasion, and chemical resistance, depending on the application.
Safety and Compliance
Consideration must be given to health and safety standards, as well as industry regulations, so the chosen coating is compliant with safety requirements and environmentally sustainable.
Cost Efficiency
While upholding quality is essential, factors like initial costs, maintenance requirements, and lifecycle performance influence the overall cost-effectiveness of the coating solution.
Maintenance Considerations for Industrial Coatings
Even the most durable coatings benefit from regular maintenance to extend their lifespan. Here are some strategies to implement:
- Routine inspections: Periodically evaluate coatings for signs of cracks, discoloration, or wear.
- Reapplication: Certain coatings may require reapplication over time for continued efficacy.
- Cleaning procedures: Follow cleaning protocols using appropriate substances to avoid damaging the coating.
Remember, adhering to a preventative maintenance schedule minimizes repair costs and system downtime.
Emerging Trends in the Industrial Coatings Industry
Technology and sustainability are driving innovation in the coatings sector. Here’s what’s on the horizon.
Smart Coatings
These coatings embed sensors to monitor the health of surfaces, providing real-time alerts for potential damage or degradation.
Eco-Friendly Coatings
Manufacturers are moving toward low-VOC and water-based formulations to reduce environmental impact.
Nanocoatings
By using nanotechnology, industrial coatings can deliver unparalleled durability, self-cleaning properties, and resistance to pollutants.
3D Printing Integration
Advanced coatings are being developed to complement 3D-printed industrial components for better adhesion and extended lifespans.
Leveraging Industrial Coatings for Tomorrow’s Industries
Industrial coatings are fundamental to innovation, efficiency, and operational safety across sectors. From revolutionizing manufacturing lines to enabling sustainable solutions, the role of coatings will only grow in the years ahead. With this overview of the different types of industrial coatings, you can make an informed decision for your business and find success.
James Manufacturing offers professional machining and fabrication services that make it easier than ever to take products, parts, and components from design to completion. With our prototype machine shop, you can get your ideas off the ground faster and for less money. Discover the power and convenience of having us as a partner!
The body content of your post goes here. To edit this text, click on it and delete this default text and start typing your own or paste your own from a different source.