10 Sheet Metal Design Mistakes You Should Avoid
Sheet metal design is vital to a wide range of manufacturing sectors, including automotive, aerospace, consumer electronics, and construction. From vehicle parts to household appliances, getting the design right is essential to ensure functionality, durability, and cost efficiency. However, even seasoned manufacturers can make mistakes in their sheet metal designs that lead to inefficiencies, increased production costs, or a compromised final product.
Recognizing and addressing these pitfalls ahead of time can save your company time and resources. To this end, we’ll explore 10 sheet metal design mistakes you should avoid, including actionable solutions and tips to help set you on the path to success.
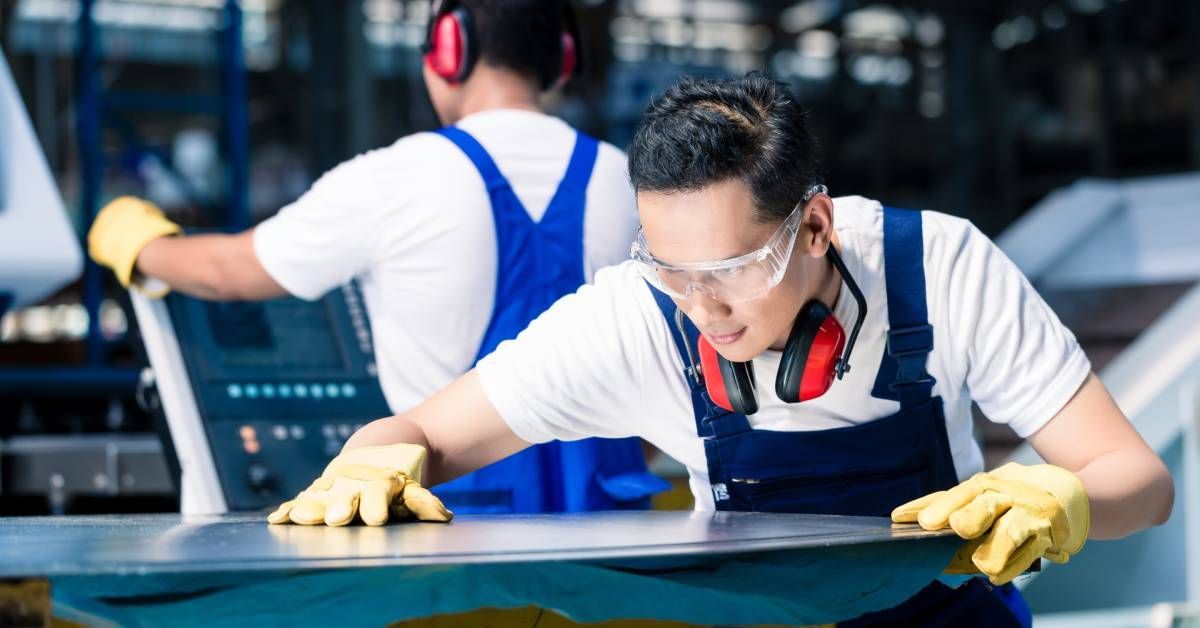
Examples of Sheet Metal Design in Different Industries
Sheet metal designs are indispensable across diverse industries. Here are just a few examples of their applications to demonstrate the importance of precision in design:
- Automotive: Cars, trucks, and other vehicles rely on sheet metal for body panels, structural reinforcements, and exhaust systems.
- Aerospace: Sheet metals are used in the wings, fuselage, and structural frames of aircraft, requiring extreme precision to minimize weight while maintaining strength.
- Consumer electronics: Devices like laptops, smartphones, and household appliances use sheet metal for enclosures and casings to provide structure and protection.
- Construction: HVAC ducts, roofing panels, and structural steel components highlight the importance of durable, well-designed sheet metal structures.
These industries show how important it is to avoid design mistakes. Now, let’s look at the most common errors made during the sheet metal design process.
10 Common Sheet Metal Design Mistakes (and How To Fix Them)
Sheet metal design is a comprehensive process with all sorts of things that can go wrong along the way. Here’s what to watch for.
1. Ignoring Material Properties
Every type of sheet metal, be it aluminum, steel, or copper, has unique properties such as tensile strength, flexibility, and corrosion resistance. Designing without considering these properties can lead to a weak or unsuitable product, resulting in cracking, warping, or difficulty during the fabrication process.
Solution
Choose materials that align with the functional requirements of the product, and establish clear communication with fabricators regarding raw material specifications.
2. Overlooking Design for Manufacturability (DFM)
A design that looks great on paper may fail during production if it’s too complex or challenging for manufacturing equipment to handle. This can lead to increased production time and costs and reduced product scalability.
Solution
Collaborate with fabrication shops early in the design phase to align your design with manufacturing capabilities.
3. Incorrect Bend Radius
Misjudging the bend radius can cause cracking or distortion in the metal. A radius that is too tight is especially problematic. If left unchecked, it can result in structural issues and material fatigue.
Solution
Follow the 1x thickness rule (bend radius should be greater than or equal to 1 times the thickness of the sheet). Always check your material’s bend tolerance guidelines.
4. Poor Hole Placement
Placing holes too close to edges or bends can weaken the structure, making the product vulnerable to damage. This means reduced product strength and potential failure during use.
Solution
Maintain proper clearance by keeping holes at least twice the material’s thickness away from edges and bends.
5. Overcomplicating Features
Designers often add unnecessary details or sharp corners that make manufacturing overly complex, resulting in increased production time, higher tooling costs, and unnecessary waste.
Solution
Simplify designs where possible, replacing sharp corners with rounded ones and removing nonfunctional details.
6. Ignoring Springback Compensation
After bending, sheet metal tends to “spring back” slightly to its original shape, which can cause deviations from the intended design.
Solution
Account for springback by overbending slightly and working with experienced fabricators to determine proper compensation levels.
7. Failing To Optimize for Weight
Unnecessarily heavy designs can result in inefficiencies, especially in the aerospace and automotive industries where weight impacts fuel efficiency. Such issues can increase costs due to material waste and reduced functionality.
Solution
Use lightweight materials where feasible, and remove excess mass with strategic cutouts, balancing strength and durability.
8. Neglecting Finishing Options
Failing to consider how finishing processes like powder coating or anodizing will affect design dimensions or durability can lead to product defects. This can potentially lower corrosion resistance and lead to improper fits.
Solution
Incorporate finishing tolerances into your design, and specify clear coating and finishing requirements.
9. Skipping Prototyping
Skipping the prototyping phase can lead to catastrophic design flaws being identified only after production has begun. This often means escalating costs, wasted materials, and delays.
Solution
Use rapid prototyping techniques, such as laser cutting, to test and refine designs early on.
10. Ignoring Tolerances
Overly tight tolerances can significantly increase manufacturing costs, while loose tolerances may result in poor-quality assemblies or even part failure.
Solution
Use realistic tolerances that ensure functionality without overburdening production processes.
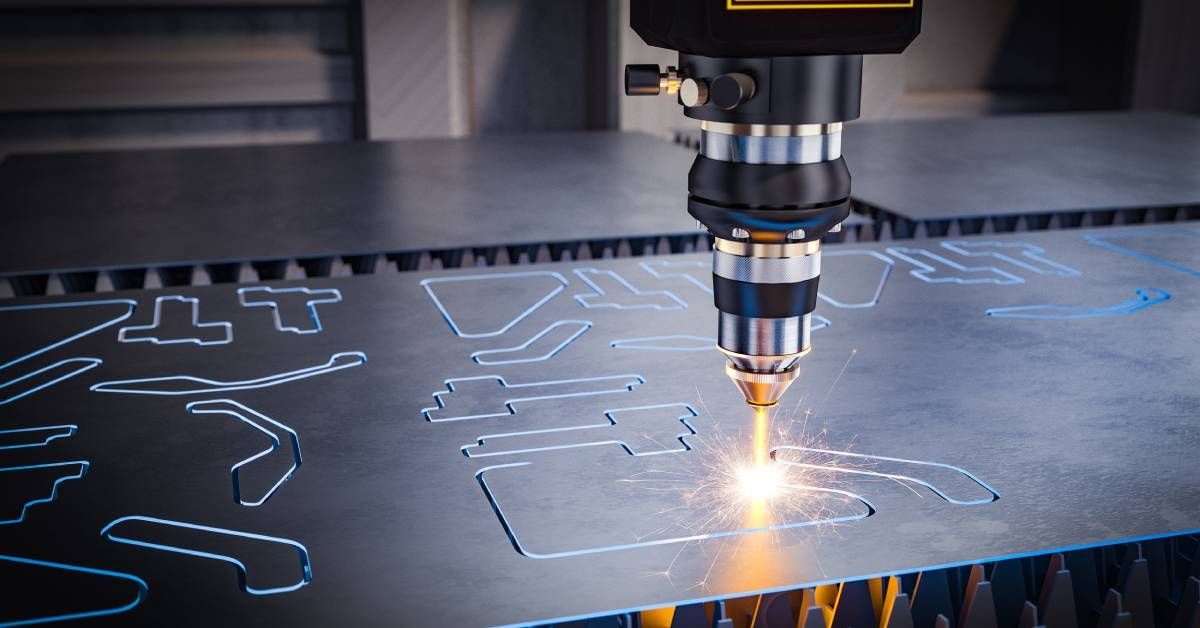
Actionable Tips for Improving Sheet Metal Designs
Implementing a few key practices can go a long way in improving your sheet metal designs. To start, collaborate with your fabrication vendor early to ensure designs are manufacturable. Invest in CAD software with sheet metal-specific features to analyze ideas before production.
For best results, use industry-standard design guidelines for aspects like blank development, bend allowances, and tolerances. By regularly reviewing past projects, you can identify patterns in design issues and improve future processes. With these tips and solutions in mind, you can avoid common sheet metal design mistakes and produce high-quality products that meet both your functional and aesthetic requirements.
Why Outsource to a Professional Fabrication Company?
Outsourcing your sheet metal fabrication to a professional shop offers several advantages. With the right professionals, you can benefit from years of manufacturing experience to avoid common mistakes. They have access to state-of-the-art tools and machinery, ensuring precision and efficiency throughout the scope of the project.
High-quality fabrication reduces scrap rates and rework expenses. Plus, professional fabricators work faster, enabling quicker product rollouts. Partnering with an experienced team allows your business to focus on its core operations while ensuring top-notch quality. Prioritizing precision and open communication with fabricators can ensure the success of your sheet metal designs.
Avoid Costly Sheet Metal Design Mistakes
Precision is key in sheet metal design, and avoiding costly errors should be a top priority for any company relying on fabricated parts or components. By avoiding these 10 sheet metal design mistakes, you can improve not only product quality but also the overall efficiency of your operations.
Need help perfecting your designs? James Manufacturing is your trusted partner for handling fabrication from start to finish. Our stainless steel fabrication services will help you achieve your vision without breaking the bank. Save time, reduce costs, and make your next project a success!