10 Common Mistakes During the Prototyping Phase
The prototyping phase is a critical step in metal fabrication. Ideas transform into tangible objects, offering manufacturers an opportunity to test, refine, and perfect designs before full-scale production. Yet, many manufacturers face hurdles during this process that delay production, inflate costs, and compromise quality.
To establish a clear path to success, learn about the ten common mistakes made during the prototyping phase. These insights could save your project time and money.
What Is the Prototyping Phase in Metal Fabrication?
Prototyping bridges the gap between concept and production. During this stage, manufacturers create a preliminary model or sample of a metal product. The overall purpose is to evaluate design feasibility, identify potential flaws, streamline production methods, and ensure that the final product meets the necessary quality standards.
Done right, prototyping offers manufacturers the chance to innovate while minimizing risk. However, when mistakes occur, they ripple through the entire production process, creating future problems.
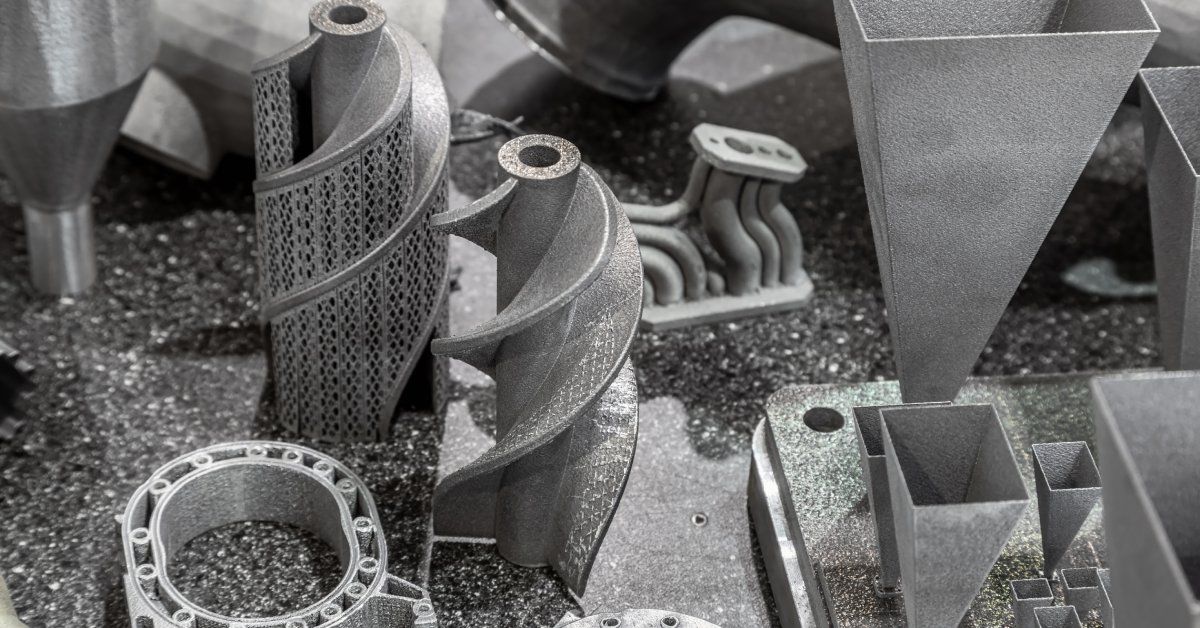
The Consequences of Prototyping Mistakes
Even small errors in the prototyping phase can snowball into major challenges.
- High costs: Flawed prototypes require revisions that increase material waste, labor hours, and retooling costs.
- Delayed timelines: Errors slow down the path to mass production and, in some cases, may delay product launches.
- Compromised quality: Shortcutting steps frequently result in products that fail to meet customer expectations or regulatory standards.
- Damaged reputation: Persistent issues during prototyping can erode customer trust and harm long-term relationships with stakeholders.
Taking the time to refine your prototype builds a solid foundation for a successful product launch and builds confidence in the final design.
Industries That Rely on Metal Fabrication Prototyping
The industries listed below benefit from the accuracy, customization, and quality control provided by metal fabrication prototyping, enabling them to deliver innovative products and solutions to their respective markets.
Automotive
The automotive industry relies on metal fabrication prototyping to develop vehicle components, such as engine parts, chassis, and body panels.
Aerospace
Metal fabrication prototyping helps in the production of aircraft parts and components, including structural elements, landing gear, and turbine engines. The durability and quality of these prototypes are incredibly important to adhere to the aerospace industry’s strict standards.
Medical
Medical equipment manufacturers use metal fabrication prototyping to produce precise and sterile instruments, implants, and devices used in surgeries, diagnostics, and patient care.
Energy and Power
Energy and power sectors create metal components for power generation systems, transmission infrastructure, and renewable energy technologies.
Construction
Metal fabrication prototyping is vital in the construction industry for developing structural components, building facades, and specialized architectural elements that require precise engineering.
Electronics
Electronics manufacturers rely on metal fabrication prototyping to produce casings, heat sinks, and other components for electronic devices, ensuring efficient thermal management.
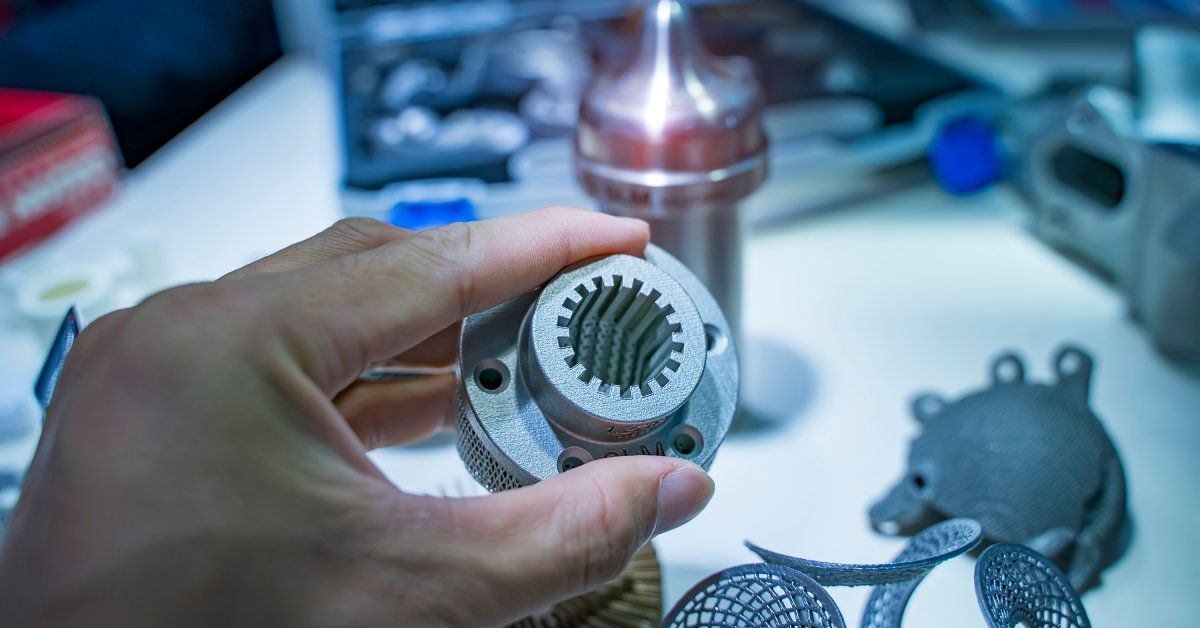
10 Common Mistakes During the Prototyping Phase
1. Lack of Communication Between Design and Production Teams
When design and production teams operate separately, misalignments are inevitable. Poor communication can result in prototypes that fail to meet design specifications, wasting valuable materials and time. Regular check-ins, collaborative tools, and consistent feedback can keep everyone on the same page.
2. Overlooking Material Selection
Materials affect the performance and longevity of products. Skipping a detailed material analysis during prototyping can lead to issues like corrosion, weakness, or increased expenses. Evaluate the properties, availability, and cost of the materials against the project’s requirements.
3. Ignoring Testing and Validation
A prototype is only as good as its ability to identify flaws in the design. Failing to subject the model to rigorous testing can lead to unnoticed hidden defects, creating larger problems during mass production.
4. Rushing the Prototyping Process
Time constraints may tempt manufacturers to rush through prototyping, but this frequently results in overlooked errors and subpar products. Rushed prototypes can force rework later in the production phase, undoing any perceived time savings.
5. Not Considering Scalability for Mass Production
A prototype might look and function perfectly, but can the design handle large-scale production? Account for factors such as tooling requirements, assembly complexity, and cost per unit to avoid unexpected expenses during production.
6. Underestimating Time and Cost
Prototyping can be more resource-intensive than expected, especially with advanced designs. Underestimations can strain budgets and delay project completion. Build contingencies into budgets and timelines.
7. Failure To Incorporate User Feedback
Ignoring input from the end users of the finished product is a missed opportunity. Their feedback ensures that the prototype aligns with user needs and expectations. Collaborate with users in early development stages to avoid costly redesigns later.
8. Using Outdated or Inefficient Methods
Continuing to rely on outdated tools or techniques that are slow, less precise, or unable to meet modern standards can compromise the quality of the prototype. Invest in updated machinery, software, or processes to deliver improved results.
9. Neglecting Documentation
Documenting every step of the prototyping process, from the materials to the test results, creates a repository of knowledge for future designs. Failing to do so can cause teams to repeat mistakes or overlook successful techniques.
10. Prioritizing Aesthetics Over Functionality
While visual appeal matters, focusing too much on aesthetics during prototyping can detract from addressing important functional aspects. Meet key performance metrics before refining aesthetic details.
Best Practices for Effective Prototyping
How can manufacturers ensure their prototyping processes are efficient, cost-effective, and successful? Use the following tips to optimize the prototyping process, maximize the value of user feedback, and deliver superior products.
Start Simple
Begin with a basic prototype to test the core functionality. This allows for quick iterations and avoids investing too much time and resources into complex designs that may need several revisions.
Iterate and Refine
Embrace an iterative approach, continuously refining the prototype based on user feedback and testing results. Incorporate learnings from each iteration to improve the design and address any shortcomings.
Test Real-World Scenarios
Simulate real-world scenarios and user interactions during testing to uncover potential oversights and validate the prototype’s performance under various conditions. This helps identify areas for improvement so you can develop a reliable product.
Seek Feedback
Regularly seek feedback from stakeholders and end users throughout the prototyping process. This iterative feedback allows for prompt adjustments and minimizes the risk of costly rework later in the development cycle.
Take Your Prototyping Process to the Next Level
For manufacturers, prototyping offers an opportunity to refine, innovate, and prepare for production. By learning from these ten common mistakes to avoid during the prototyping phase and implementing various best practices, you can achieve smooth workflows, reduced costs, and superior products.
Are you searching for a metal machining shop that can strengthen your prototyping process? At James Manufacturing, we’re experts in fabrication, CNC, and welding. No matter how big your business is, our expertise is sure to offer substantial value to your operations.