How Is CNC Machining Used in the Renewable Energy Industry?
With manufacturing processes evolving rapidly, renewable energy stands at the forefront of sustainable development. But did you know that CNC machining is pivotal in this green revolution? Serving businesses from automotive to aerospace, it’s a game-changer for renewable energy.
But how is CNC machining used in the renewable energy industry? We’ll discuss these questions and more, giving you insights that you can turn into opportunities.
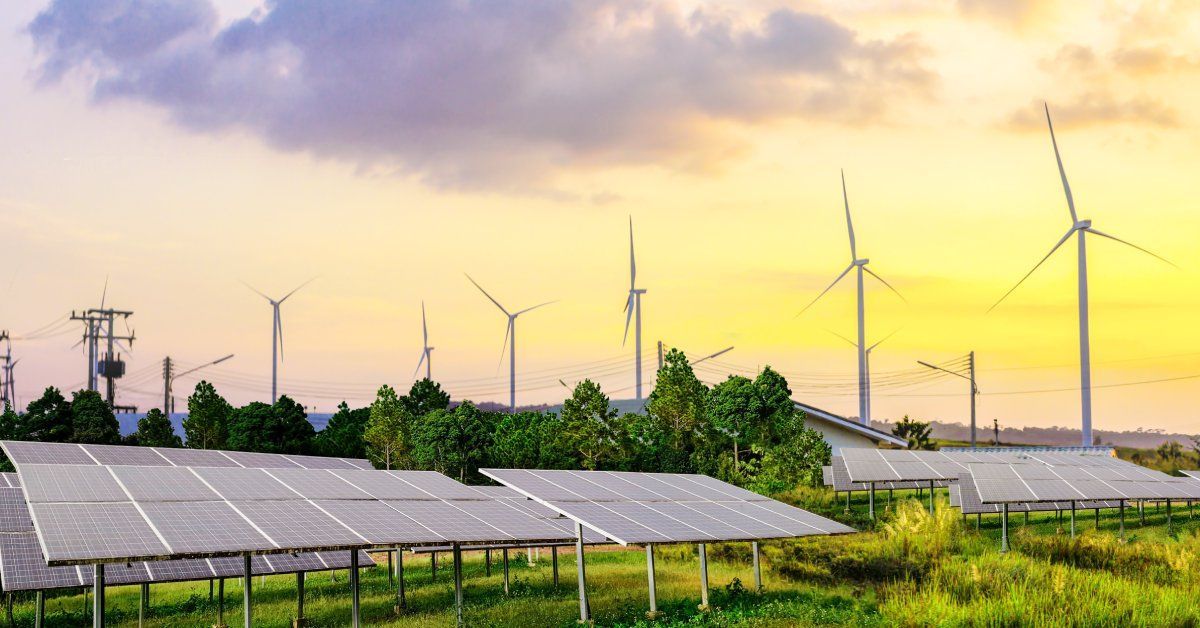
Understanding CNC Machining and Its Green Impact
From wind turbines to solar panels, the renewable energy industry relies heavily on precision manufacturing. This is where CNC machining comes into play. But what exactly is CNC machining, and why is it relevant to renewable energy?
How It Works
CNC stands for “computer numerical control.” In essence, CNC machining involves using computers to control machine tools. Machines like lathes, mills, and routers craft objects by removing material with high precision. With its automated control, CNC machining produces consistent, accurate parts, minimizing waste and maximizing efficiency.
The Advantages
One advantage of CNC machining is its ability to produce complex designs with pinpoint accuracy. This precision is crucial for renewable energy components, which often must withstand harsh environmental conditions. Additionally, CNC machining is highly scalable, making it perfect for both prototypes and mass production. Lastly, automation reduces human error, leading to higher-quality products and less material waste.
Relevance to Renewable Energy
CNC machining is indispensable in the quest for efficient and reliable renewable energy solutions. From wind and solar to hydroelectric and geothermal, there’s no space that can’t be improved by quality machined parts. By aiding in the precise creation of these key components, CNC machining drives advancements in sustainable technologies.
Applications in the Renewable Energy Sector
The renewable energy sector is diverse, encompassing multiple power sources. Let’s explore these applications in detail.
Wind Turbine Manufacturing
Wind turbines are technological marvels, towering over landscapes with intricate designs. Wind turbine components, including blades, gears, and towers, require absolute precision. CNC machining ensures these parts are crafted to exact specifications, enhancing the turbine’s productivity and lifespan. The method also aids in producing lightweight yet durable materials, essential for modern turbines.
Solar Panel Production
Solar panels capture sunlight and convert it into electricity, requiring components that can endure variable weather conditions. CNC machining can produce the metal frames, brackets, and mounting systems necessary for solar installations. Precision is vital here, as even minor discrepancies can reduce energy capture. CNC machines ensure that every piece fits perfectly, optimizing solar energy collection.
Hydroelectric Parts Fabrication
Hydroelectric power uses the flow of water to generate electricity. Turbines and generators demand components that function flawlessly under pressure. CNC machining is perfect for crafting the intricate parts needed, like turbine blades and casings, ensuring durability and efficiency. CNC machining’s ability to produce large volumes of identical high-quality parts makes it indispensable for hydroelectric projects.
Geothermal Station Maintenance
Geothermal energy taps into the Earth’s internal heat, requiring robust equipment that can handle extreme temperatures and pressures. CNC machining creates precision parts needed for geothermal stations, such as heat exchangers and pumps. By building these components to exacting standards, CNC machining aids in maintaining operational efficiency and longevity.
Hydrogen Plant Components
The future of clean energy might very well lie in hydrogen. Producing hydrogen requires complex systems where each part must work seamlessly. CNC machining helps manufacture critical components like compressors and storage tanks. With its precision, CNC machining ensures these parts meet strict safety and performance standards for hydrogen energy’s success.
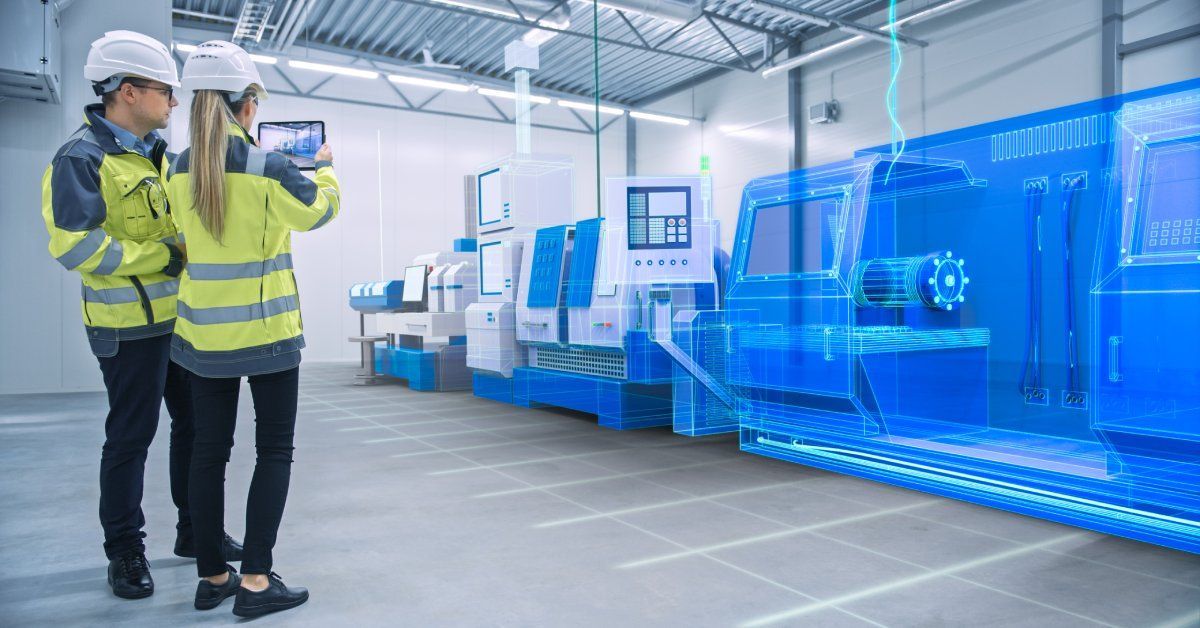
CNC Machining’s Future in Renewable Energy
The intersection of CNC machining and renewable energy is ripe with potential. With advancements in both fields, the future looks promising.
Advanced Machine Learning Algorithms
Integrating machine learning into CNC machining processes will allow for predictive maintenance and real-time optimization, leading to even higher efficiency and reduced downtime in renewable energy component production.
Sustainable Materials Processing
Future CNC machines will be designed to process newer sustainable materials that are lightweight and strong, essential for constructing more efficient wind turbines and solar panels.
Additive Manufacturing Integration
Combining CNC machining with additive manufacturing technology will enable the creation of more intricate and robust parts, reducing waste and conserving resources in the production of renewable energy components.
Improved Energy Efficiency
Next-generation CNC machines will consume significantly less energy, thanks to advancements in motor technology and process optimization, aligning with the sustainability goals of the renewable energy sector.
Precision Enhancement Technologies
Innovations in precision technologies, such as laser-guided cutting and improved sensor integration, will ensure even greater accuracy in part creation, boosting the performance of renewable energy systems.
Remote Monitoring and Control
Future CNC systems will feature enhanced remote monitoring capabilities, allowing operators to oversee and control processes from anywhere, increasing operational efficiency and flexibility in manufacturing.
AI-Driven Design Automation
The use of artificial intelligence in design processes will streamline the creation of complex components, optimizing designs for functionality and efficiency right from the initial stages of manufacturing.
By exploring these innovations and investing now, businesses can secure their future in whatever industry they operate in.
Prefabricated vs. Custom Parts in Renewable Energy
When navigating the production and maintenance of renewable energy systems, manufacturers must decide between using prefabricated and custom parts. Each approach offers distinct advantages and trade-offs, impacting performance, cost, and flexibility.
Prefabricated Parts
Prefabricated parts are mass-produced, standardized components designed for broad applications. They are often more accessible due to their availability and typically cost less than custom-made parts. These parts can be ideal for initial deployments where budget constraints and shorter lead times are priorities.
Prefabricated parts also benefit from a proven track record of reliability, having been rigorously tested across similar systems. However, their standardization may result in suboptimal performance if the part doesn’t meet the specific requirements of unique or highly specialized machinery.
Custom Parts
In contrast, custom parts are engineered to meet specific project needs, allowing for tailored solutions that can significantly enhance system efficiency and longevity. They provide flexibility in design, accommodating unique system configurations and innovative ideas.
Custom CNC machining enables the production of parts with intricate geometries and precise tolerances that standard parts cannot achieve. While this personalization can drive up costs and lead times, the investment often pays off through increased performance, reduced operational downtime, and the potential to unlock innovations in renewable energy technology.
The Hybrid Approach
Deciding between prefabricated and custom parts involves balancing immediate project requirements against long-term operational goals. In many cases, a hybrid approach that incorporates both prefabricated components for general use and custom parts for critical areas can offer the best of both worlds, keeping costs manageable.
The Lasting Impact of CNC Machining on Green Energy
The significance of CNC machining in the renewable energy industry cannot be overstated. It’s a technology that not only supports current innovations but also paves the way for future advancements. By enabling the creation of high-quality, precise components, CNC machining is a catalyst for change in the renewable energy sector. It ensures that systems are efficient, durable, and capable of meeting the growing energy demands of the world.
Understanding and leveraging CNC machining can lead to significant advantages for companies invested in renewable energy. Our custom CNC machining services are designed to meet your every need. By adopting this technology, the path to a sustainable future becomes clearer and more attainable.