How Can Industrial Coatings Help Prevent Corrosion?
Corrosion prevention maintains the integrity and safety of industrial operations. Failure to address the issue can result in costly repairs, operational downtime, and sometimes catastrophic breakdowns. A corrosion prevention plan for businesses is about sustaining profitability and upholding safety standards.
So, how can industrial coatings help prevent corrosion? This post uncovers the role of industrial coatings in combatting corrosion and guides businesses in harnessing their full potential.
Understanding the Causes of Corrosion
Corrosion is a complex electrochemical reaction where metals like iron and steel oxidize and form compounds such as rust. While some may see corrosion as a simple rusting process, it has far-reaching implications in industrial settings.
For instance, corrosion weakens equipment’s structural integrity, increasing the risk of failure. This is particularly concerning for industries like oil and gas, manufacturing, and construction, where metal infrastructure is vital for operations.
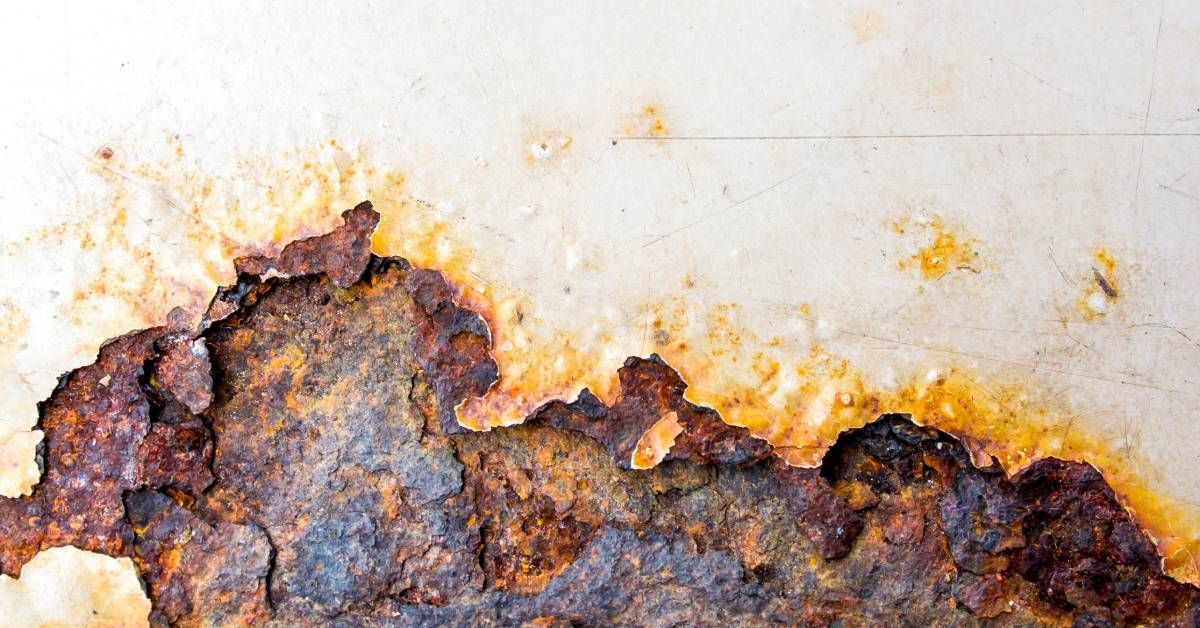
Factors Contributing to Corrosion
Many factors contribute to the onset of corrosion, including:
- Moisture: One of the primary catalysts for corrosion, moisture in the air can condense on metal surfaces, leading to oxidation and rust formation.
- Chemical exposure: Industrial chemicals, acids, and salts accelerate corrosion when they encounter metal surfaces.
- Temperature extremes: Higher temperatures can cause chemical reactions, while lower ones can lead to the formation of condensation, both of which contribute to corrosion.
- Environmental conditions: Factors such as salt water, air pollution, and humidity levels impact corrosion rates.
- Material properties: The type of metal, its composition, and protective coatings or treatments applied can influence its susceptibility to corrosion.
- Mechanical stress: Continuous stress or vibrations on metal components can cause microcracks, providing entry points for corrosive agents.
- Poor maintenance: Inadequate maintenance and cleaning allow corrosive substances to accumulate on surfaces, exacerbating corrosion problems.
Understanding these factors is essential for implementing effective corrosion prevention strategies, such as choosing the right industrial coatings.
Industrial Coatings Explained
Industrial coatings prevent corrosion by forming a physical barrier that shields the metal surface from corrosive agents. This barrier blocks moisture and oxygen, essential components of the corrosion process. Additionally, some coatings contain corrosion inhibitors that neutralize erosive elements, enhancing the protective capabilities of the coating.
Coatings also improve the aesthetic appeal of metal surfaces, offering a clean, polished look. This dual function of protection and aesthetics makes industrial coatings a valuable solution for businesses looking to maintain the visual and structural integrity of their assets.
Benefits of Using Industrial Coatings
Industrial coatings offer various benefits that manufacturers can take advantage of to improve the quality of their products.
Increased Equipment Lifespan
One of the most significant benefits of industrial coatings is the extended lifespan of equipment and structures. Coatings minimize wear and tear by preventing corrosion and reducing the need for frequent repairs or replacements. This longevity translates to cost savings, as businesses can avoid the expenses associated with constant maintenance and downtime.
Reduced Maintenance Costs
Industrial coatings are an investment in preventive maintenance. While the initial application may incur costs, the long-term savings make up for it. Coated surfaces require less frequent cleaning, repair, and replacement, allowing businesses to allocate resources more efficiently. This cost-effectiveness is a compelling reason for industries to adopt coating solutions.
Improved Safety
Corrosion weakens metal structures, yes, but it also poses safety risks. In industries like oil and gas, corrosion-induced leaks or structural failures can lead to hazardous situations. Industrial coatings enhance safety by preserving the integrity of critical infrastructure, reducing the likelihood of accidents, and promoting compliance with safety standards.
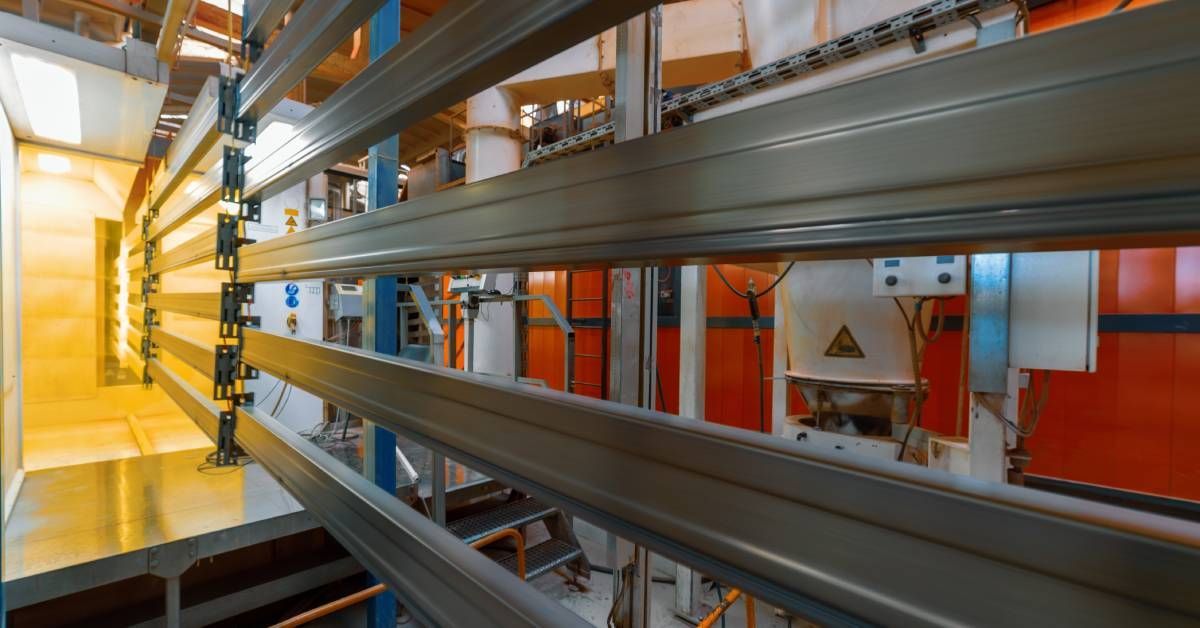
Types of Industrial Coatings
Industrial coatings come in various types, each designed to address specific corrosion challenges:
- Epoxy coatings: With powerful adhesion and strong chemical resistance, epoxy coatings are often used in marine and industrial environments. They provide a durable protective layer that can withstand harsh conditions.
- Polyurethane coatings: These coatings offer high flexibility and abrasion resistance, making them suitable for surfaces that experience mechanical stress. Polyurethane coatings also provide strong UV resistance.
- Zinc-rich coatings: Serving as a sacrificial layer, zinc-rich coatings protect steel surfaces from corrosion. They’re particularly effective in marine and humid environments where metal exposure is high.
- Acrylic coatings: Acrylic coatings are favored for their fast-drying properties and good color retention. They’re often used for aesthetic purposes but also provide environmental protection.
- Alkyd coatings: These coatings work well in mild environments and are valued for their ease of application and cost-effectiveness. Alkyd coatings are typically used in less aggressive industrial environments.
- Fluoropolymer coatings: Renowned for their superior nonstick and low-friction properties, fluoropolymer coatings are employed where resistance to corrosion and high temperatures is essential.
- Ceramic coatings: Offering exceptional thermal resistance, ceramic coatings are used in high-temperature settings, protecting metal surfaces from extreme heat and oxidation.
- Intumescent coatings: These coatings are used primarily for fireproofing materials. They expand in high-heat environments, creating an insulating layer that protects structural components during fires.
Industrial coatings are specially formulated to provide a protective barrier between the metal surface and its environment.
Tips for Selecting the Right Coating
Finding the coating that fits your needs will provide the highest quality results. Here’s what you need to know:
- Assess environmental conditions: Determine the specific environmental factors your structures will encounter, such as humidity, temperature extremes, chemical exposure, and sunlight, to select coatings designed to withstand these conditions.
- Consider material compatibility: Check that the coating is compatible with the type of metal and materials used in your infrastructure to prevent adverse reactions and encourage optimal adhesion.
- Evaluate longevity and durability: Choose coatings known for their longevity and durability, particularly those that offer extended protection and require minimal maintenance over time.
- Prioritize ease of application: Select coatings that are easy to apply and adaptable to your operational environment, reducing downtime and application costs.
- Consult industry standards: Refer to industry regulations and standards to ensure that the coatings meet safety and performance criteria specific to your industry.
- Seek professional guidance: Engage with coating professionals or suppliers who can recommend the best solutions tailored to your specific needs and provide technical support throughout the application process.
Investing in Better Corrosion Prevention Strategies
Industrial coatings are indispensable tools in safeguarding vital infrastructure and assets. Understanding how industrial coatings can help prevent corrosion allows businesses to extend the lifespan of their equipment, reduce maintenance costs, and improve operational safety. Remember, investing in industrial coatings is about enhancing efficiency, sustainability, and performance.
Businesses that adopt innovative solutions gain a competitive edge, no matter what type of industry they’re in. If you’re looking for a
custom machining shop that can help you bring your products to life, James Manufacturing is here to help you achieve success. Take advantage of our professional expertise and enhance your operations.