Comparing 5 Common Metal Cutting Techniques
Metal cutting is a common manufacturing process across numerous industries, playing a key role in modern engineering and fabrication. No matter what types of products you’re creating, metal cutting is the backbone of producing parts that fit together seamlessly.
Understanding and appreciating the different ways of working with metal can help manufacturers make better decisions during the production process. We’ll compare five common metal cutting techniques and help you understand their benefits, limitations, and suitability for different applications.
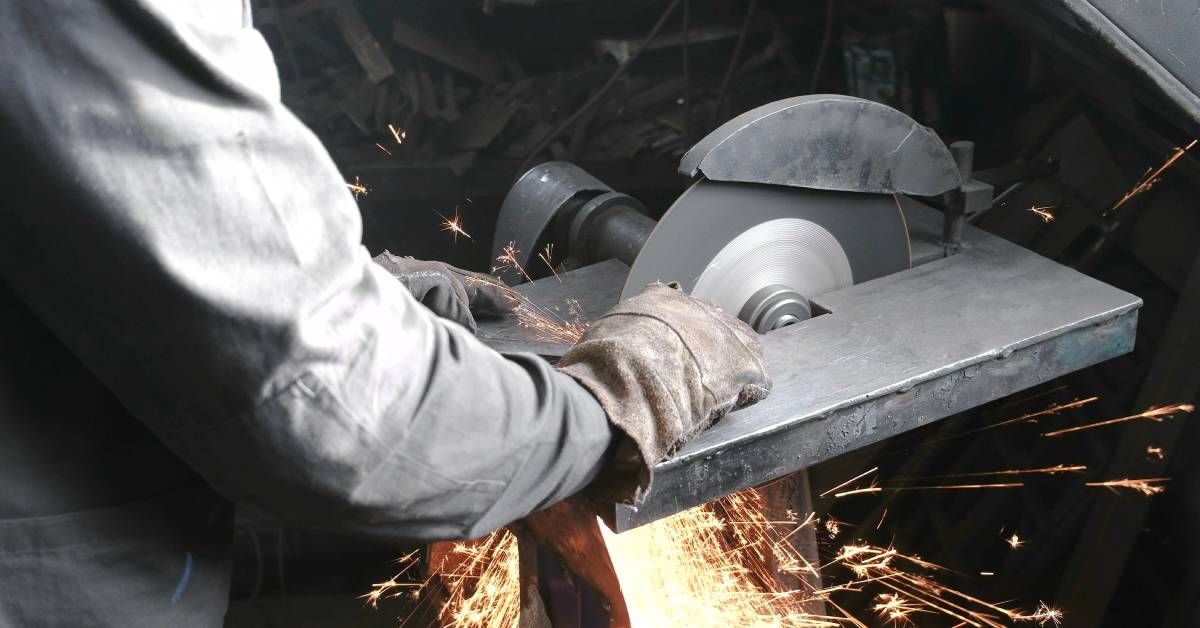
The Role of Metal Cutting Across Industries
Cutting metal precisely and efficiently is essential for production across a variety of sectors; it affects everything from timelines to costs. Each technique offers unique advantages and addresses the needs of different sectors:
- In the automotive industry, metal cutting is essential for manufacturing car bodies, engines, and various automotive components.
- Precision cutting techniques are vital for crafting aircraft parts, such as turbine blades and structural components, in the aerospace industry.
- In the construction industry, metal cutting creates steel frameworks, bridges, and other structural elements.
- Delicate metal cutting is employed in the electronics industry to produce components for electronic devices, including circuit boards and housings.
- In the shipbuilding industry, cutting techniques are useful for shaping metal sheets and components for ships and submarines.
- Artists use metal cutting to create detailed sculptures and installations.
- High-precision cutting is crucial for producing surgical instruments and medical devices.
- Metal cutting is fundamental in producing molds and dies for the tool and die industry.
Overview of Popular Metal Cutting Techniques
Understanding the following techniques provides a foundation for improved decision-making in manufacturing.
1. Plasma Cutting
Plasma cutting uses a high-speed stream of ionized gas to melt and cut through metals. This technique is ideal for its speed and ability to cut through thick materials. Plasma cutting is useful in automotive repair, industrial construction, and metal fabrication shops.
This method is popular for its versatility; professionals can cut through various types of metal, including stainless steel, aluminum, and copper. It offers a good balance of speed and precision, making it excellent for many applications. However, it may not deliver the cleanest edges, and workpieces may require additional finishing.
2. Waterjet Cutting
Waterjet cutting uses a high-pressure water jet that contains abrasive materials to slice through metal. Known for its precision and ability to cut without heat, it is perfect for projects requiring fine detail. Waterjet cutting is common in aerospace, automotive, and artistic industries.
The technique stands out for its ability to cut complex shapes with smooth edges, making it ideal for materials sensitive to high temperatures. While it may be slower than plasma cutting, its precision and versatility in cutting various materials make it invaluable. Plus, it is environmentally friendly because it uses only water and abrasives.
3. Laser Cutting
Laser cutting uses a focused laser beam to melt, burn, or vaporize materials, achieving high precision and accuracy. This method is perfect for making intricate cuts, such as with electronic, automotive, and aerospace component manufacturing.
Laser cutting excels in producing detailed work with tight tolerances. It provides clean cuts with minimal waste, enhancing efficiency in production. Keep in mind that laser cutting can be slow on thick materials and tends to be more expensive than other cutting methods due to equipment costs and operation.
4. EDM (Electrical Discharge Machining)
EDM involves using electrical discharges to erode metal along precise paths. It is ideal for mold-making, tool and die industries, and aerospace applications.
This method is indispensable when cutting complex contours or delicate internal structures. EDM works best with conductive materials and provides an excellent surface finish. However, it can be slower than other techniques.
5. CNC Machining
Computer numerical control (CNC) machining utilizes computer-controlled tools to remove material and shape metal components. This technique is prevalent in automotive, aerospace, and industrial machinery fabrication for its versatility and precision.
CNC machining offers a wide range of capabilities, from simple cuts to complex 3D shapes. It’s highly adaptable and useful for both prototyping and production. Keep in mind that it’s not the fastest technique and can be costly due to machine setup and operational expenses.
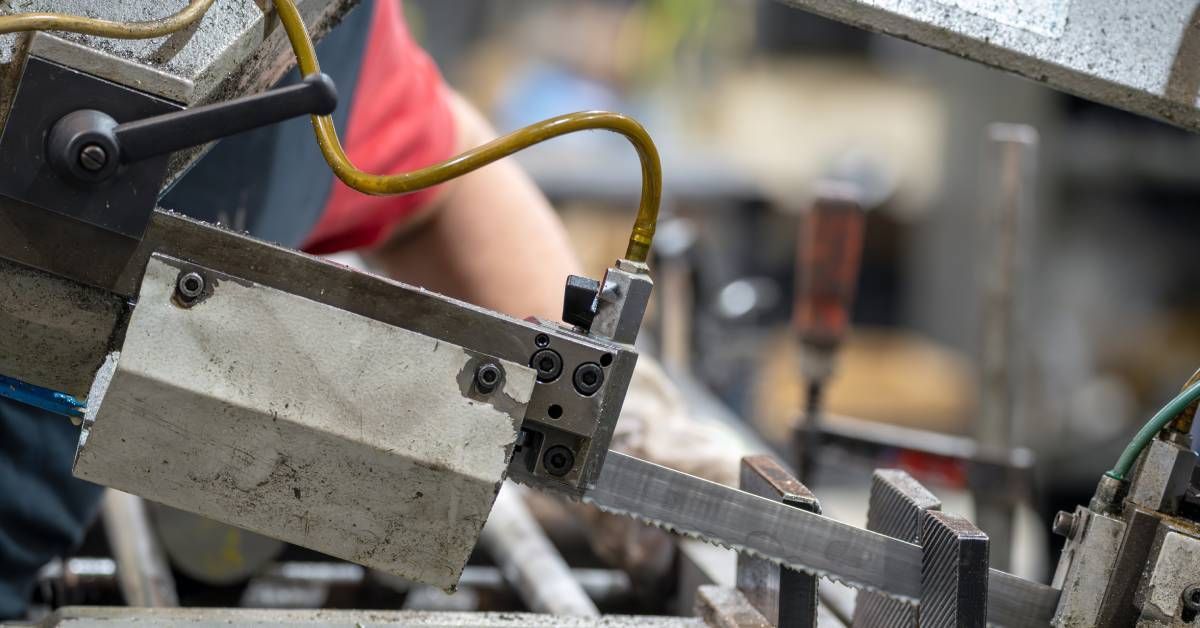
Factors To Consider When Choosing a Metal Cutting Technique
Understanding each metal-cutting technique and its benefits helps businesses maintain competitiveness and meet challenges head-on. Considering these factors will help you select the most appropriate metal-cutting technique for specific needs, ensuring efficient production and optimal results.
- Some materials require different cutting methods. For example, plasma cutting is effective for thick metals, such as stainless steel and aluminum, while waterjet cutting is suitable for delicate materials sensitive to heat.
- If your project requires precision and intricate details, consider laser cutting or EDM, which provide excellent accuracy and surface finish.
- The urgency of project timelines may dictate the cutting method. Plasma cutting is speedy, which is beneficial for rapid production. EDM may be slower yet offers greater precision.
- Budget constraints will influence your choice. CNC machining and laser cutting may have higher upfront costs due to equipment expenses, but they offer long-term cost efficiency through minimal waste and high-quality results.
- The desired finish and edge quality of the final product can determine the metal cutting technique. Waterjet cutting produces smooth edges that require little post-processing.
- For creating parts with complex geometries or complex internal structures, EDM and CNC machining are suitable due to their ability to execute intricate cuts with high accuracy.
- Waterjet cutting is environmentally friendly since it uses a mixture of water and abrasives, making it preferable for reducing the carbon footprint of the manufacturing process.
Create a More Innovative Metal Manufacturing Process
Comparing the five most common metal-cutting techniques can positively impact your project’s success. By understanding each method’s strengths and limitations, you can choose the best approach for your needs. Staying updated on industry developments can lead to innovative and efficient manufacturing processes. Exploring these techniques and their applications is valuable for improving your metal-cutting operations.
Are you looking for a metal fabrication shop to help you make the right choice between the different cutting techniques? At James Manufacturing, we offer personalized fabrication services so that you’re happy with the final result. Discover the benefits of working with a professional partner you can trust!